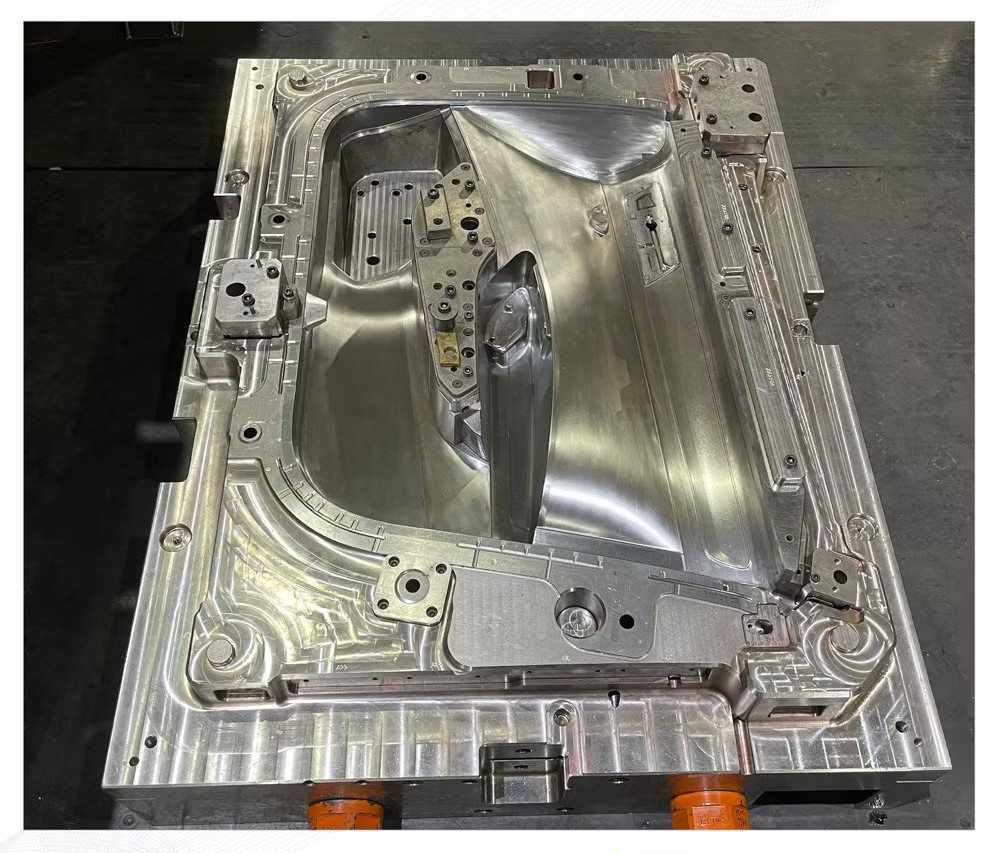
Injection molding is a highly effective manufacturing process for producing door panels, widely used in the automotive, furniture, and construction industries. This process enables the creation of durable, aesthetically appealing, and functional door panels with high precision. By leveraging advanced materials and mold designs, injection molding meets the demanding requirements for door panels in terms of strength, design flexibility, and cost efficiency.
Process of Injection Molding Door Panels
Design and Material Selection
- Design: Engineers use CAD software to create 3D models of the door panel, incorporating features like ribs for structural support and textured surfaces for aesthetics.
- Material: Selection is based on criteria such as impact resistance, thermal stability, and lightweight properties.
Tooling Preparation
- A mold is created, typically from steel or aluminum, designed to replicate the exact shape of the door panel. High precision ensures proper fit and finish.
Injection Molding
- Material Melting: Thermoplastic resin is melted and injected into the mold cavity at high pressure.
- Filling and Cooling: The molten plastic flows into the mold, filling every detail of the design. Cooling channels within the mold ensure uniform solidification.
- Ejection: Once cooled, the door panel is ejected, leaving a finished product ready for additional processing.
Post-Processing
- Secondary operations, such as trimming, painting, or adding foam backing, may be performed to enhance functionality and aesthetics.
Key Features of Injection-Molded Door Panels
Lightweight Construction
Using lightweight plastics reduces the overall weight of the product while maintaining structural integrity, a critical factor in automotive applications for improving fuel efficiency.Aesthetic Appeal
Injection molding enables a variety of surface finishes, from smooth to textured, as well as the integration of custom colors and decorative inlays.Functional Integration
Door panels can include molded-in features such as speaker grilles, storage compartments, and electronic mounts, reducing the need for assembly and additional components.Cost Efficiency
The high repeatability of injection molding minimizes material waste and production costs, especially for high-volume manufacturing.
Applications of Injection-Molded Door Panels
Automotive Industry
- Interior door panels for cars, trucks, and SUVs, designed with integrated armrests, controls, and sound insulation.
- Panels are made to be lightweight, durable, and visually appealing.
Furniture and Cabinets
- Decorative panels for doors on cabinets, closets, or furniture pieces, often featuring custom textures or patterns.
Building and Construction
- Durable and weather-resistant panels for residential and commercial doors, often used for outdoor applications.
Advantages of Injection Molding for Door Panels
- High Productivity: The rapid cycle times of injection molding make it ideal for large-scale production.
- Precision Engineering: Enables tight tolerances for parts that must fit seamlessly with other components.
- Material Efficiency: Excess material can often be recycled, reducing waste.
- Customization Options: Offers flexibility in design, texture, and functionality to meet diverse customer needs.
Challenges and Solutions
Complex Tooling Requirements:
- Challenge: Molds for large, intricate panels can be expensive and time-consuming to produce.
- Solution: Modular tooling and advanced simulation tools help optimize mold designs and reduce costs.
Warping and Defects:
- Challenge: Improper cooling can lead to warping or surface imperfections.
- Solution: Uniform cooling channels and precise process control ensure defect-free panels.
Material Selection:
- Challenge: Selecting the wrong material can compromise durability or aesthetics.
- Solution: Material testing and consultation with suppliers ensure optimal performance.