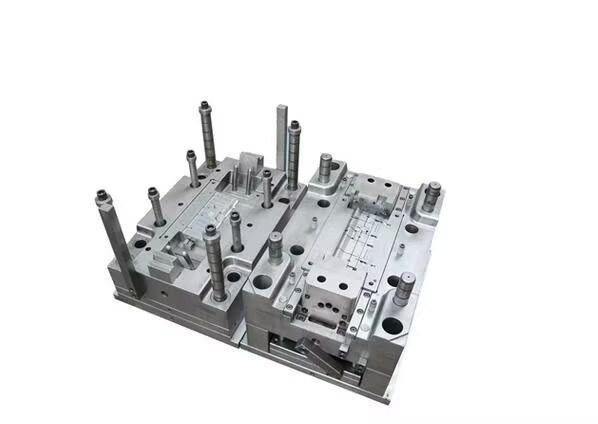
Injection molding is a critical manufacturing process in the electronics industry, providing a reliable method for creating durable, lightweight, and precise components. The process is widely used for producing enclosures, connectors, switches, and various structural parts that are essential for electronic devices.
High Precision and Complex Designs
Electronics components often require intricate shapes and tight tolerances to fit into compact devices. Injection molding enables manufacturers to achieve high levels of precision, ensuring that parts are compatible with circuit boards and other components. The ability to create detailed designs with consistent quality makes this process indispensable for producing small-scale and complex electronics parts.
Material Versatility
A wide range of materials, such as thermoplastics and thermosetting polymers, are used in injection molding for electronics. Popular materials include ABS (Acrylonitrile Butadiene Styrene) for durability and heat resistance, polycarbonate for its transparency and impact strength, and nylon for flexibility and strength. These materials provide electrical insulation, fire resistance, and mechanical stability, which are crucial for electronics applications.
Cost Efficiency in Mass Production
Injection molding is particularly cost-effective for high-volume production, a common requirement in the electronics sector. Once the mold is created, the process allows for rapid manufacturing of thousands or millions of identical components with minimal material waste. This scalability makes it an ideal choice for producing parts like USB connectors, smartphone cases, and appliance housings.
Enhanced Durability and Performance
The electronics industry demands components that can withstand heat, electrical currents, and physical stresses. Injection molding provides a way to manufacture parts with high mechanical strength and thermal resistance. Materials can also be engineered to include additives for flame retardancy, UV protection, or enhanced conductivity.
Lightweight Designs
Weight reduction is critical in electronics, especially for portable devices like smartphones, laptops, and wearables. Injection molding allows for the use of lightweight materials without compromising structural integrity, aiding in the design of ergonomic and portable products.
Sustainable Practices
With growing concerns over environmental sustainability, injection molding for electronics has embraced eco-friendly practices. Recyclable plastics and bio-based polymers are increasingly used to reduce the environmental impact of production. Additionally, the precision of the process minimizes waste, and advancements in mold design and materials extend the lifecycle of electronic components.