Injection molding is one of the most efficient and widely used manufacturing processes for producing parts in high volumes, particularly in industries like automotive, medical devices, electronics, consumer goods, and packaging. The process involves injecting molten material (usually plastic) into a mold cavity, which is then cooled to form a solid part. When scaled for high-volume production, injection molding offers precision, consistency, and cost-efficiency, making it an ideal solution for producing large quantities of parts with tight tolerances and intricate designs.
1. What is Injection Molding?
Injection molding is a manufacturing process where material (such as thermoplastics, thermosets, or elastomers) is melted and injected into a mold cavity under high pressure. The mold, which is a precise negative of the desired part shape, cools the material, solidifying it into the final product.
Key components of the injection molding process include:
- Injection Unit: This is where the raw material is fed into the machine and heated to a molten state.
- Mold: The mold is a precision tool that forms the shape of the part. It consists of two halves—one stationary and one movable.
- Clamping Unit: This part of the machine holds the mold halves together during the injection process and ensures the mold does not separate under pressure.
2. Why is Injection Molding Ideal for High-Volume Production?
Injection molding is particularly well-suited for high-volume production due to several key factors:
Speed and Efficiency: Once a mold is created, the cycle time for injection molding is relatively short—typically ranging from 10 seconds to a few minutes depending on part complexity. This rapid cycle time enables manufacturers to produce thousands or even millions of parts per day.
Precision and Consistency: Injection molding is known for producing parts with high precision and tight tolerances, ensuring uniformity across large production runs. This consistency is critical for industries like automotive and electronics, where part accuracy is essential.
Complex Geometries: Injection molding can produce parts with intricate shapes, undercuts, and internal features that may be difficult or expensive to achieve using other manufacturing processes.
Material Versatility: A wide range of materials can be used in injection molding, including various thermoplastics, thermosets, and composites. This versatility allows manufacturers to select the best material for the performance and cost requirements of the part.
Automation and Scalability: The injection molding process can be highly automated, reducing labor costs and increasing production efficiency. Once the molds are designed and the machines are set up, production can be scaled to meet high-volume demands without significant increases in cost or complexity.
3. Steps Involved in High-Volume Injection Molding
The process of injection molding can be broken down into several key steps:
Mold Design and Tooling: The first step is to design the mold. This is a critical phase that directly affects the quality and speed of production. For high-volume production, molds are often made of durable steel or aluminum and are carefully engineered to ensure they can withstand thousands or even millions of cycles.
Material Preparation: The raw material, typically in the form of pellets or granules, is fed into the injection molding machine’s hopper. The material is then heated to a molten state, which is necessary for injection into the mold.
Injection: The molten material is injected into the mold cavity under high pressure using a screw or plunger mechanism. The material fills the mold, taking the shape of the cavity.
Cooling: Once the mold is filled, the material is allowed to cool and solidify. The cooling time can vary depending on the material and the part’s thickness.
Ejection: After cooling, the mold is opened, and the part is ejected from the mold cavity. This process is often automated to minimize downtime and ensure quick turnaround.
Post-processing: After ejection, parts may require additional processes like trimming, surface finishing, or assembly. This is usually done to remove excess material (flash), improve aesthetics, or prepare the parts for further assembly.
4. Key Factors in High-Volume Injection Molding
Several factors contribute to the success of high-volume injection molding production:
Mold Durability: High-volume production requires molds that can withstand thousands or even millions of cycles. Steel molds are often preferred for their longevity, while aluminum molds may be used for less demanding applications or when rapid prototyping is needed.
Cycle Time: The efficiency of the injection molding machine is crucial for high-volume production. Short cycle times, typically under a minute, help keep production costs low and meet the high-output requirements.
Quality Control: Consistent quality control measures are necessary to ensure parts meet specifications over long production runs. Automated inspection systems and sampling methods are often used to ensure high-quality output.
Material Selection: The choice of material is critical for both performance and cost considerations. High-volume production may involve optimizing material cost, while also ensuring that the selected material meets the functional requirements of the part.
Energy Efficiency: Given the scale of high-volume injection molding, energy efficiency can significantly impact overall production costs. Machine advancements have made injection molding machines more energy-efficient, helping reduce operational costs.
5. Advantages of Injection Molding for High-Volume Production
Cost-Effective for Large Quantities: Although the upfront costs for mold creation can be high, once the mold is made, the per-unit cost for injection molding drops significantly with higher production volumes. This makes it an attractive option for producing large quantities of parts.
Customization: The process allows for a wide range of design variations, allowing companies to customize parts to meet specific needs without significant modifications to the tooling.
Reduced Waste: Because injection molding is a highly precise process, material waste is minimized, making it more environmentally friendly compared to other manufacturing methods.
Repeatability: Injection molding is highly repeatable, meaning that parts produced in large batches will maintain consistent quality and dimensions.
6. Challenges in High-Volume Injection Molding
Despite its many advantages, there are challenges associated with high-volume injection molding:
Initial Investment: The cost of designing and producing molds can be high, especially for complex or large parts. However, this cost is amortized over high-volume production.
Material Limitations: While many materials can be used in injection molding, certain materials may not be compatible with the process, limiting options in some cases.
Tool Wear: Molds can wear out over time, especially in high-volume production. Regular maintenance and replacement of molds can be necessary to maintain part quality.
Production Line Set-Up Time: Although the injection molding process is efficient once in full operation, setting up and fine-tuning production lines can take time and effort, especially for complex parts or new designs.
7. Applications of Injection Molding in High-Volume Production
Injection molding is used in a wide range of industries for high-volume production of parts. Some common applications include:
Automotive Parts: Components like dashboards, bumpers, and interior panels are often produced using injection molding for high-volume manufacturing.
Consumer Electronics: Injection molding is used to produce housings for smartphones, computers, televisions, and other electronic devices.
Medical Devices: Components like syringes, surgical instruments, and drug delivery devices are made using injection molding due to the need for precision and hygiene.
Packaging: Many packaging materials, such as bottles, caps, and containers, are produced through injection molding due to its cost efficiency and speed.
8. Future of High-Volume Injection Molding
As technology evolves, high-volume injection molding continues to benefit from advancements in materials, mold design, and machine efficiency. New innovations in 3D printing, material science, and automation are pushing the boundaries of what can be achieved with injection molding, allowing for even more complex designs, reduced waste, and enhanced sustainability.
Injection molding remains a cornerstone of modern manufacturing, especially for high-volume production. Its combination of speed, precision, and cost-efficiency makes it an invaluable tool for producing parts in large quantities. As industries continue to demand higher performance and faster turnaround times, the injection molding process will likely evolve further to meet these needs while maintaining its position as a leading method in mass production.
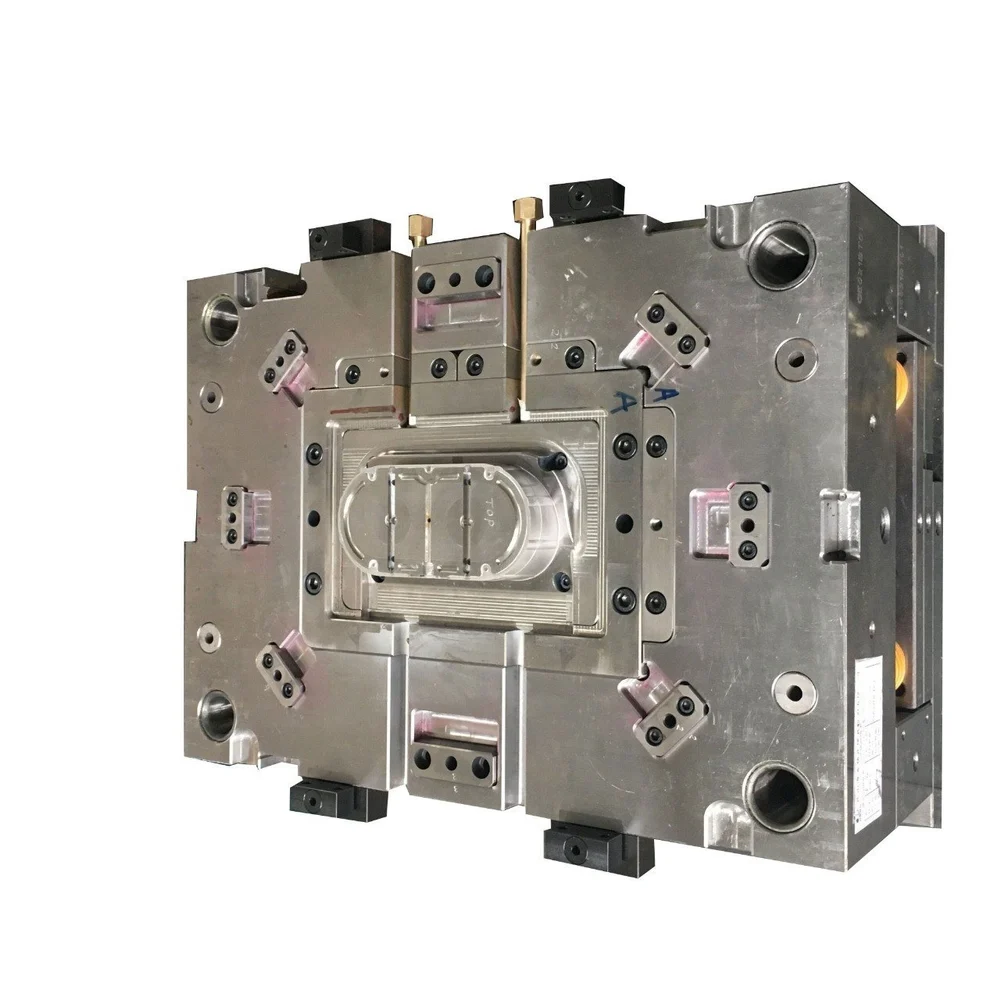