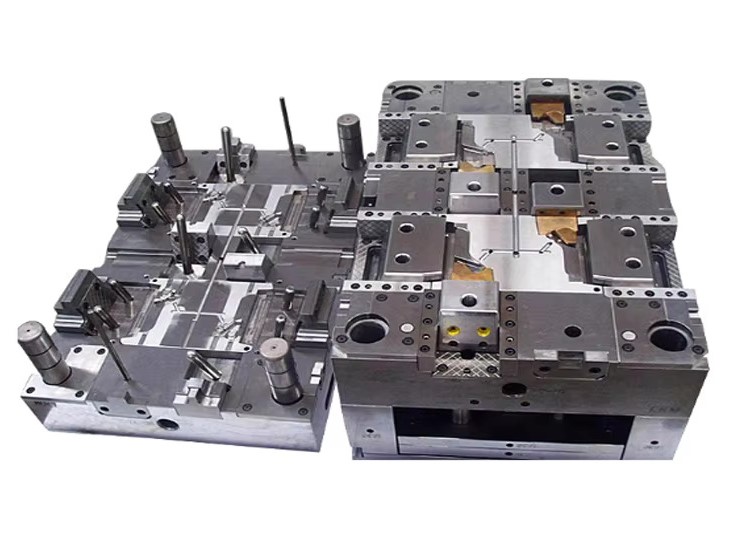
Injection molding is a highly versatile manufacturing process used to produce intricate and small parts with exceptional precision and consistency. It involves injecting molten material, typically plastic or thermoplastic, into a custom-designed mold cavity under high pressure. Once cooled and solidified, the part is ejected from the mold, ready for use or further assembly. The process is highly scalable, making it ideal for producing large volumes of identical parts efficiently.
For small and complex components, injection molding is particularly advantageous due to its ability to create intricate geometries that would be challenging or impossible with other manufacturing techniques. Modern advancements in mold design, such as micro-molding and precision machining, allow for tolerances as tight as a few microns, ensuring even the most delicate features are reproduced accurately. This makes injection molding a preferred method in industries such as medical devices, electronics, and automotive, where miniaturization and high precision are critical.
The material selection in injection molding further enhances its suitability for complex parts. Engineers can choose from a wide range of thermoplastics, including high-performance polymers with excellent mechanical, thermal, or chemical properties. Additives and fillers can also be incorporated to enhance strength, flexibility, or other desired characteristics. This versatility ensures that the final product meets specific application requirements without compromising quality or durability.
Moreover, the cost-effectiveness of injection molding stems from its efficiency in producing large quantities of parts with minimal material waste. Innovations such as multi-cavity molds and hot-runner systems further optimize production times and reduce costs. For small, complex parts, these features ensure that the process remains economical even for high-precision applications.