Injection molding plays a critical role in the automotive industry, particularly in the manufacturing of steering wheels and airbag components. This process allows for high-volume, precision production of parts that meet stringent safety and performance standards.
1. Overview of Injection Molding
Injection molding is a manufacturing process used to produce parts by injecting molten material into a mold. It is highly favored in the automotive industry due to its efficiency, repeatability, and ability to produce complex geometries with tight tolerances.
Materials Used:
Thermoplastics (e.g., Polypropylene, Polyurethane, ABS)
Thermosetting plastics (for heat resistance)
Reinforced composites (for added strength and rigidity)
2. Injection Molding in Steering Wheel Manufacturing
The steering wheel is a critical driver interface component that must offer durability, tactile comfort, and safety. It typically comprises a metal frame overmolded with plastic and/or polyurethane foam.
Process:
Metal Core Fabrication: The inner frame is often made from magnesium or steel, providing structural strength.
Overmolding: A layer of plastic or polyurethane is injected over the core to form the desired ergonomic shape.
Surface Finishing: Leather, synthetic covers, or textured plastics may be applied for aesthetics and comfort.
Advantages:
High precision for ergonomic shapes
Integration of design features like grip contours and control interfaces
Cost-effective for mass production
3. Injection Molding for Airbag Components
Airbag systems include various molded parts such as the cover, housing, and internal supports. These components must be precisely engineered to deploy correctly during a crash.
Key Components Molded:
Airbag Covers: Designed to split along predetermined lines upon deployment. Often made from ABS or PC/ABS blends.
Housing Units: Contain the inflator and folded airbag. Require high mechanical strength.
Guide Rings and Retainers: Help deploy the airbag smoothly.
Special Considerations:
Tear Line Design: Injection molds are engineered to create “tear seams” that break cleanly and reliably during deployment.
Material Selection: Must withstand extreme temperatures and pressures, as well as UV exposure and aging.
Dimensional Stability: Critical to ensure proper assembly and function of the airbag module.
4. Quality and Safety Standards
Components produced via injection molding for steering wheels and airbags must comply with stringent automotive standards:
ISO/TS 16949
FMVSS (Federal Motor Vehicle Safety Standards)
OEM-specific requirements
Testing includes:
Environmental aging
Drop and impact testing
Deployment simulation
Material and dimensional inspections
5. Benefits of Injection Molding in Automotive Safety Components
Consistency: Maintains tight tolerances across large production volumes
Cost-Effectiveness: Ideal for mass production
Customization: Supports integration of design and functional features
Lightweighting: Helps reduce vehicle weight for better fuel efficiency
6. Future Trends
Use of Bio-based and Recycled Materials to meet sustainability goals
Advanced Molding Techniques like multi-material molding and gas-assisted injection
Integration with Electronics, such as haptic feedback or steering wheel controls
Conclusion
Injection molding is indispensable in the production of steering wheel and airbag components, offering precision, safety, and cost-efficiency. As automotive design continues to evolve, so too will the materials and techniques used in this vital manufacturing process.
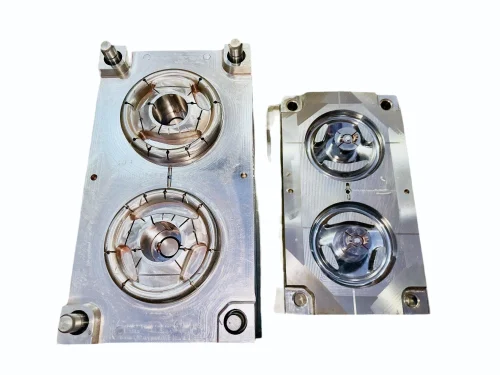