Injection molding is a widely used manufacturing process for producing plastic parts by injecting molten material into a mold. Its efficiency and precision make it ideal for both low-volume and high-volume production, though the approaches and economics differ significantly between the two.
1. Tooling Differences
Low-Volume Production:
Tooling Material: Often uses softer, less durable materials like aluminum or soft steel (P20).
Tooling Cost: Lower initial cost; faster and cheaper to fabricate.
Lead Time: Shorter mold production time—ideal for rapid prototyping or pilot runs.
High-Volume Production:
Tooling Material: Hardened steel (H13, S7), built for longevity and durability.
Tooling Cost: High upfront investment due to complex machining and durability.
Lead Time: Longer setup and testing times, but sustainable over millions of cycles.
2. Cost Considerations
Low-Volume:
Per-Part Cost: Higher per unit due to less amortization of tooling costs.
Best For: Prototyping, bridge tooling, market testing, and custom/specialty products.
Flexibility: Easier to modify tooling or switch designs between runs.
High-Volume:
Per-Part Cost: Very low due to economies of scale.
Best For: Mass production of consistent parts (e.g., automotive, packaging).
ROI: Tooling cost is spread over a large quantity, making it more economical in the long run.
3. Production Speed & Cycle Time
Low-Volume:
Faster mold fabrication but may use slower or manual processes for molding.
Shorter runs mean quicker changeovers between projects.
High-Volume:
Optimized for speed and efficiency with automated processes and robotics.
Longer cycle time investment pays off with high-speed, high-output systems.
4. Design and Material Flexibility
Low-Volume:
More design flexibility due to simpler molds.
Easier to test various materials, geometries, and modifications.
High-Volume:
Requires robust design validation upfront to avoid costly mistakes.
Limited design changes once production starts due to mold rigidity.
5. Applications
Low-Volume:
Startups and R&D
Medical device prototyping
Aerospace and defense (custom, low-quantity parts)
Market validation
High-Volume:
Consumer electronics
Automotive parts
Packaging (bottles, caps, containers)
Household goods
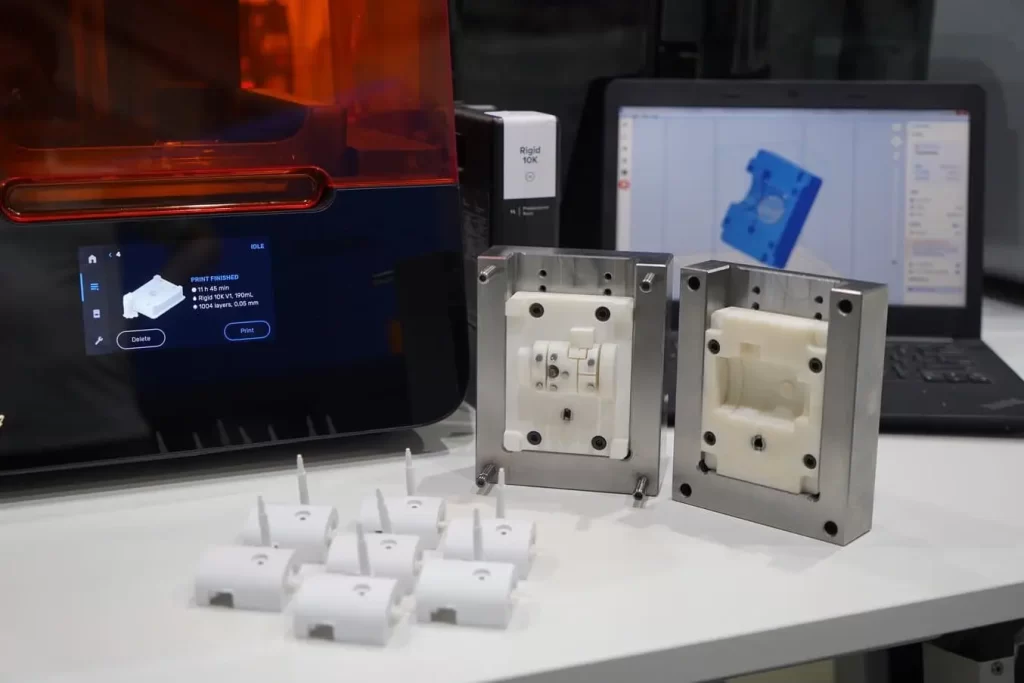