Injection molding is a critical manufacturing process for producing high-precision plastic parts used across various industries, including automotive, medical, electronics, and consumer goods. Injection molding simulation software has become an essential tool in the design, testing, and optimization of injection molding processes. This software enables manufacturers to predict and optimize the behavior of molten plastic within a mold before physical production begins.
Benefits of Injection Molding Simulation Software
Cost and Time Savings
Reduced Prototyping Costs: Traditional trial-and-error methods in injection molding require multiple physical prototypes, which can be expensive and time-consuming. Simulation software helps identify potential design flaws or inefficiencies early, reducing the need for physical prototypes.
Shortened Development Cycle: Simulation software allows designers to evaluate multiple design variations and processing parameters quickly, speeding up the development cycle and enabling faster time-to-market for products.
Improved Design Accuracy and Optimization
Precise Prediction of Part Behavior: Simulation software can predict how materials will flow, cool, and solidify in a mold, providing insights into issues like air traps, weld lines, and material shrinkage. This leads to better design decisions and reduces the risk of defects.
Enhanced Mold Design: By simulating different mold designs, designers can determine the most effective mold configuration, gate placement, and cooling channels, ensuring optimal part quality and efficient cycle times.
Better Material Selection
Performance Prediction: Different materials have different behaviors during injection molding. Simulation software helps assess the flow and cooling properties of various materials in specific mold designs, enabling manufacturers to select the most suitable material for their application.
Optimizing Material Use: Simulation allows manufacturers to determine the most efficient use of material, minimizing waste and optimizing material cost, which can be a significant factor in large-scale production.
Risk Reduction
Minimized Production Issues: By simulating the injection molding process, manufacturers can identify potential issues, such as insufficient filling, air traps, or uneven cooling, that may lead to defects like warping, sink marks, or surface imperfections. This allows for corrective actions before production begins.
Enhanced Quality Control: By running multiple simulation scenarios, manufacturers can identify and fix issues that could lead to part defects, ensuring better consistency and higher product quality in mass production.
Energy Efficiency
Optimization of Process Parameters: By simulating different process parameters such as injection speed, pressure, and cooling time, the software can help identify the most energy-efficient settings. This contributes to reduced energy consumption and cost savings.
Virtual Testing and Process Validation
Design Verification: Before any physical mold is built, designers can virtually test their designs using simulation. This can lead to more reliable verification of the part’s performance and moldability without the risk and expense of physical trials.
Testing Extreme Conditions: Simulation software can also test how parts behave under extreme conditions, like high pressures or varying temperatures, ensuring robustness in real-world applications.
Limitations of Injection Molding Simulation Software
High Initial Cost
Expensive Software and Training: The initial investment in high-quality injection molding simulation software can be substantial. Moreover, the software often requires specialized training to use effectively, adding to the overall cost. For smaller companies or startups, this can be a barrier to entry.
Licensing Fees: Many simulation software packages are licensed annually, and the cost of maintaining these licenses can add up over time.
Complexity and Learning Curve
Requires Expertise: While the software can offer powerful insights, it often requires a deep understanding of injection molding principles and expertise in using the software effectively. A skilled engineer is needed to interpret simulation results correctly and make informed decisions.
Complex Interface: The complexity of simulation tools may overwhelm new users. Understanding the software’s interface and advanced features can take significant time and effort.
Accuracy and Assumptions
Dependence on Input Quality: The accuracy of simulation results depends on the quality of the input data, including material properties, machine parameters, and mold design. Any inaccurate or incomplete input can lead to misleading results.
Simplified Models: Although the software can simulate complex behaviors, it still relies on simplifications and assumptions to reduce computation time. These simplifications may not always represent the real-world behavior of materials or processes accurately, leading to discrepancies between simulated and actual results.
Limited by Software Capabilities
Simulation Limitations: Certain software packages may lack the ability to simulate highly complex, multi-material processes or advanced injection molding techniques, such as overmolding, insert molding, or multi-shot molding. In these cases, the simulation software may not provide an accurate or complete picture of the process.
Finite Element Modeling (FEM) Constraints: While FEM is a powerful tool used in injection molding simulations, it may still struggle with modeling some phenomena accurately, particularly when it comes to intricate fluid dynamics or multi-phase behavior, which can affect the precision of the simulation.
Processing Power and Time
High Computational Resources: Advanced simulations, especially those involving intricate geometry or long production cycles, require significant computational resources. The simulation process may take hours or even days, depending on the complexity of the model, which can delay design iterations.
Long Simulation Times for Large Projects: For larger-scale projects, simulation times can be quite lengthy, potentially limiting the ability to quickly run multiple iterations of design changes.
Potential for Overreliance
Overconfidence in Results: While simulation software is a valuable tool, it is not infallible. Relying solely on simulated results without validating them through real-world testing can be risky, as certain factors may not be accurately captured in the simulation, such as tool wear or the effects of mold aging.
Missed Real-World Variables: Variables such as material inconsistencies, changes in ambient conditions, and unforeseen manufacturing imperfections may not be fully accounted for in the software, leading to potential discrepancies in the final product.
Conclusion
Injection molding simulation software is a powerful tool that offers a wide range of benefits, from cost savings to improved part quality. By predicting how a part will behave in the mold, manufacturers can make more informed design decisions, optimize processes, and reduce the likelihood of defects. However, the software comes with limitations, including high costs, the need for skilled operators, and potential inaccuracies in certain scenarios. To fully capitalize on the advantages of simulation software, manufacturers should consider it as part of a broader design and testing strategy that includes real-world testing and validation.
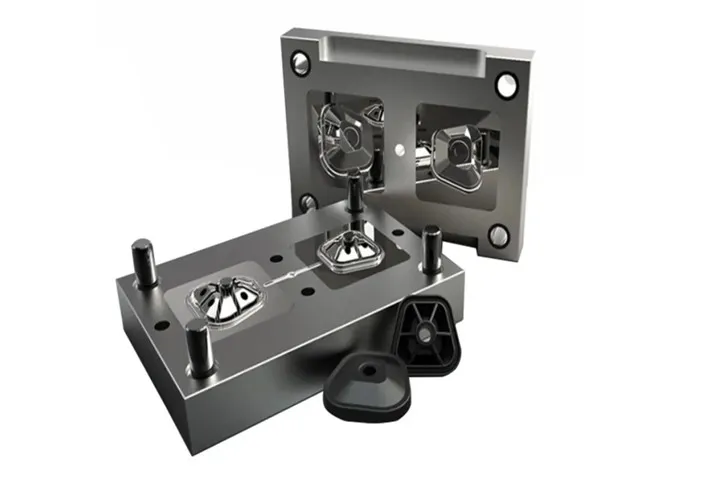