Injection molding surface finishing techniques refer to processes applied to mold surfaces or molded parts to achieve desired textures, appearances, or functional properties. These finishes can range from smooth, mirror-like surfaces to intricate textures that enhance grip, aesthetics, or functionality.
1. Purpose of Surface Finishing
Aesthetic Appeal: Enhances the look and feel of the final product.
Functional Improvement: Improves grip, wear resistance, or paint adhesion.
Defect Reduction: Minimizes visual defects such as sink marks or weld lines.
Branding and Labeling: Enables logos or product info to be textured directly into parts.
2. Common Surface Finishing Techniques
A. Polishing
Purpose: Achieves a high-gloss, mirror-like surface finish.
Method: Manual or machine polishing using abrasives and polishing compounds.
Standards: SPI (Society of the Plastics Industry) grades such as SPI-A1 (high gloss) to SPI-D3 (rough).
Applications: Optical parts, lenses, high-gloss consumer products.
B. Texturing
Purpose: Adds patterns or textures for aesthetic or functional reasons.
Method: Etching or blasting mold surfaces using lasers, chemicals, or mechanical means.
Types:
Chemical Etching: Uses acid or chemicals to create controlled patterns.
Laser Texturing: Provides precision micro-patterning.
Bead Blasting: Uses glass beads or abrasives to create matte or satin finishes.
Applications: Automotive interiors, tool handles, electronic device housings.
C. EDM (Electrical Discharge Machining) Texturing
Purpose: Produces fine, controlled textures or rough surfaces.
Method: Uses electrical sparks to erode the mold surface.
Advantages: Suitable for hard materials and complex shapes.
Applications: Mold cavities for matte finishes or non-slip surfaces.
D. Sandblasting / Grit Blasting
Purpose: Creates a uniform matte or satin texture.
Method: High-pressure abrasive blasting (sand, aluminum oxide).
Applications: Industrial parts, enclosures, or when post-painting is required.
E. Mold Coatings
Purpose: Enhances mold surface durability and part release.
Types:
Nickel or Chrome Plating: Increases wear resistance and smoothness.
PVD Coating (Physical Vapor Deposition): Adds hard, decorative coatings.
Applications: High-volume production, precision parts.
3. Surface Finish Standards
SPI (Society of the Plastics Industry): U.S. standard with grades from A (glossy) to D (textured).
VDI (Verein Deutscher Ingenieure): German standard used internationally, indicating texture levels from VDI 12 (smooth) to VDI 45 (rough).
Mold-Tech: Proprietary texturing system with standardized texture patterns.
4. Factors Influencing Surface Finishing Choice
Material type (ABS, PC, PP, etc.)
Product application and environment
Mold design complexity
Production volume
Cost constraints
Desired visual or tactile characteristics
5. Post-Molding Surface Treatments (Optional)
Painting or Coating: For aesthetics or protection.
Pad Printing or Laser Marking: For logos or labels.
Vapor Polishing: Especially for clear plastics like polycarbonate.
Conclusion
Surface finishing in injection molding is a critical step that not only defines the appearance but also impacts performance, functionality, and marketability of the product. By selecting the right technique, manufacturers can enhance the value and usability of their molded parts.
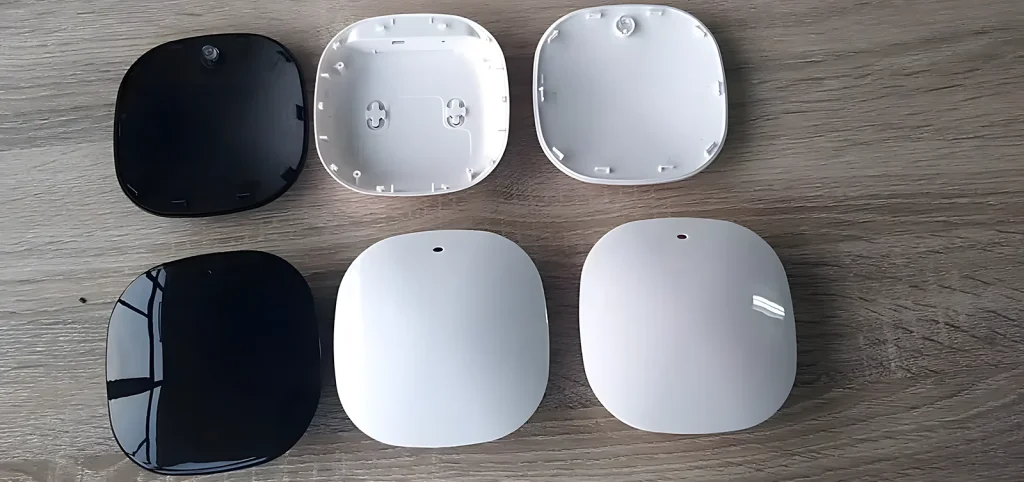