Injection molding is a widely used manufacturing process for producing precise and complex plastic components in large volumes. When combined with high-performance plastics, it offers enhanced mechanical, thermal, and chemical properties, making it suitable for demanding applications across industries such as aerospace, medical, automotive, and electronics.
What Are High-Performance Plastics?
High-performance plastics, also known as engineering thermoplastics, exhibit superior strength, heat resistance, chemical resistance, and dimensional stability compared to commodity plastics. Common examples include:
PEEK (Polyether Ether Ketone)
PPS (Polyphenylene Sulfide)
LCP (Liquid Crystal Polymer)
PES (Polyethersulfone)
PAI (Polyamide-imide)
PEI (Polyetherimide)
Why Use High-Performance Plastics in Injection Molding?
1. Thermal Stability
These materials can withstand high continuous use temperatures (often above 250°C), making them ideal for under-the-hood automotive parts or aerospace components.
2. Chemical Resistance
They are resistant to harsh chemicals, acids, and solvents, essential in medical and chemical processing applications.
3. Mechanical Strength
High stiffness, impact resistance, and fatigue endurance make them suitable for structural and load-bearing applications.
4. Dimensional Precision
Excellent dimensional stability allows for tight tolerances, critical for electronic connectors or medical devices.
Key Considerations in Injection Molding of High-Performance Plastics
1. High Processing Temperatures
These materials require higher melt and mold temperatures, often above 300°C. Specialized molds and heating systems are essential.
2. Tooling Requirements
Tooling must withstand thermal expansion and pressure. Hardened steel tools with precise temperature control are typically used.
3. Moisture Sensitivity
Many high-performance polymers are hygroscopic and must be thoroughly dried before molding to avoid defects like splay or bubbles.
4. Cycle Time
Higher processing temperatures often lead to longer cycle times, impacting productivity and cost. Process optimization is crucial.
Applications
Medical: Surgical instruments, sterilizable components, implants
Automotive: Gears, fuel system components, under-hood parts
Aerospace: Interior components, brackets, cable insulation
Electronics: Connectors, circuit components, high-heat insulation
Industrial: Pump components, seals, valves
Advantages Over Metal
High-performance plastics offer a viable alternative to metals due to:
Weight reduction
Corrosion resistance
Complex part geometries via molding
Lower production costs in large volumes
Challenges and Solutions
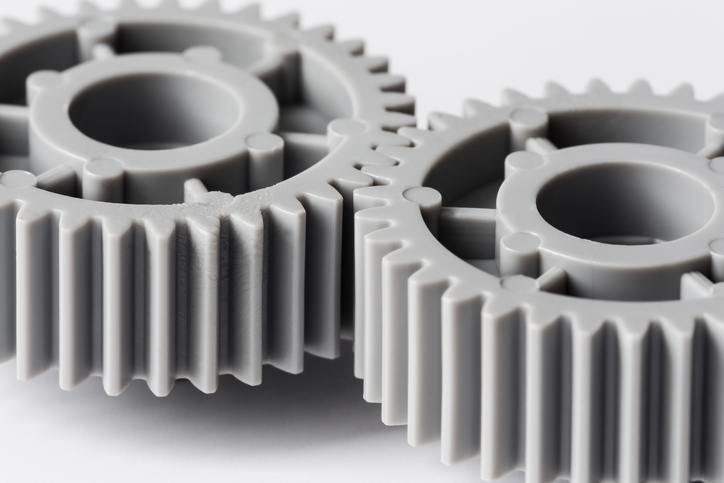