The automotive industry continually evolves to meet the demands for fuel efficiency, sustainability, and cost reduction. One effective strategy is the use of lightweight polymer molds in the manufacturing of vehicle components. These molds not only streamline production but also help reduce the overall weight of vehicles, contributing to improved fuel efficiency and lower emissions.
What Are Polymer Molds?
Polymer molds are tools made from engineered plastic materials designed to shape or form automotive components, often through processes like injection molding, compression molding, or resin transfer molding. They are increasingly used in place of traditional metal molds (e.g., steel or aluminum) for specific applications.
Benefits of Lightweight Polymer Molds
Reduced Weight
Polymer molds are significantly lighter than their metal counterparts, making them easier to handle and install, especially in low- to medium-volume production settings.Lower Manufacturing Costs
Compared to metal molds, polymer molds are often cheaper to produce and maintain. They also require less energy during processing due to their lower thermal conductivity.Faster Production Cycles
Because polymers heat up and cool down faster than metals, cycle times can be reduced, increasing throughput.Corrosion Resistance
Polymer molds are resistant to rust and corrosion, extending their usable lifespan and reducing maintenance.Customization and Design Flexibility
Polymers offer high versatility in design, allowing for complex geometries and features that would be difficult or expensive to machine in metal.
Applications in Automotive Manufacturing
Prototype Development: Ideal for short-run prototypes due to lower tooling costs and faster turnaround times.
Interior Components: Used for dashboards, trim panels, and consoles.
Non-Structural Parts: Perfect for components that don’t require high mechanical strength but benefit from weight reduction.
Electric Vehicles (EVs): Widely used in EVs where weight savings directly contribute to range extension.
Common Polymer Materials Used
Polyurethane (PU)
Epoxy Resins
Thermoplastics (e.g., ABS, Nylon, Polycarbonate)
Fiber-Reinforced Polymers (FRP)
These materials can be tailored to match mechanical, thermal, and chemical resistance requirements of various automotive parts.
Challenges and Considerations
Durability: Polymer molds may wear faster than metal ones in high-volume or high-pressure applications.
Heat Resistance: Some polymers may deform or degrade under high temperatures, limiting their use in certain molding processes.
Material Compatibility: Not all polymers are suitable for every automotive material or process.
Future Trends
3D-Printed Polymer Molds: Additive manufacturing allows for rapid prototyping and customization.
Sustainable Polymers: Development of biodegradable or recycled polymers aligns with green manufacturing goals.
Hybrid Tooling: Combining polymer and metal inserts for better performance and cost efficiency.
Conclusion
Lightweight polymer molds represent a growing trend in automotive manufacturing, offering a cost-effective, energy-efficient, and adaptable solution for modern vehicle production. While they may not replace metal molds in all scenarios, their benefits in specific applications make them an essential tool in achieving lightweight design goals, especially as the industry moves toward electric and sustainable mobility.
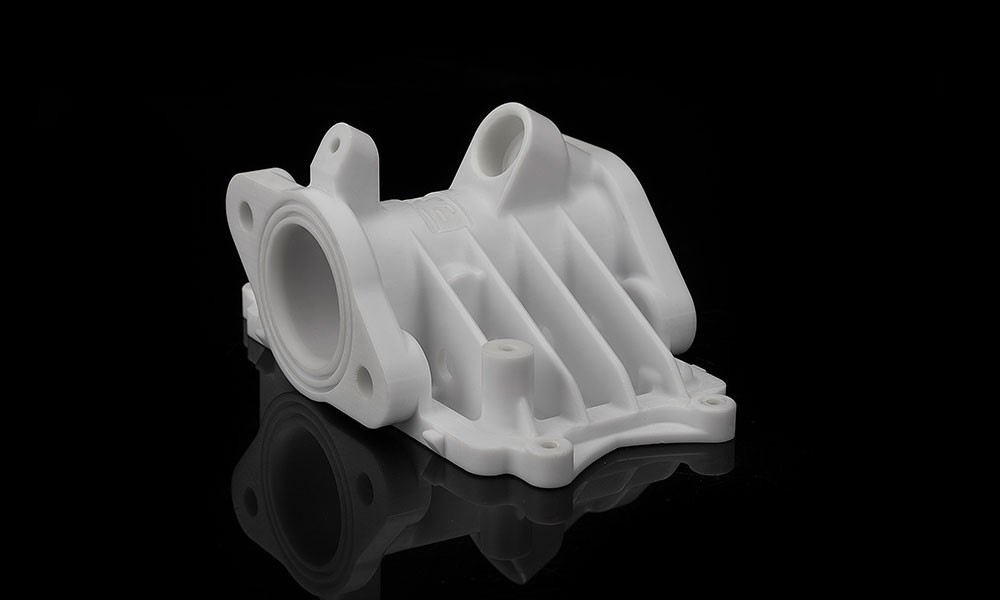