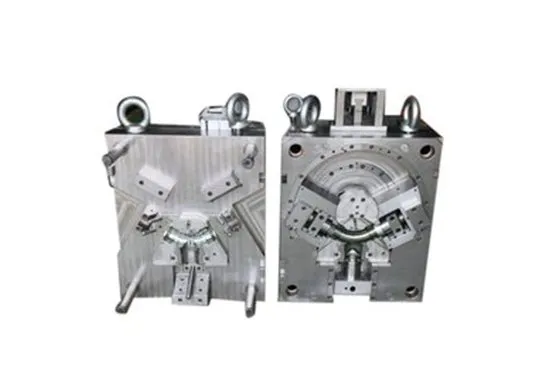
Mold flow analysis is a critical process in the manufacturing of PVC (polyvinyl chloride) products, providing insights into material flow, part design, and tooling efficiency. This simulation technique uses advanced software to predict how molten PVC will fill a mold cavity, helping to identify and mitigate potential issues before production begins. The process enhances product quality, reduces waste, and minimizes production costs.
Understanding Material Behavior
PVC has unique properties, including high viscosity and sensitivity to shear and temperature. Mold flow analysis accounts for these characteristics, modeling the material’s behavior under specific molding conditions. This ensures optimal processing parameters, such as temperature, injection speed, and pressure, are established to avoid defects like warping, shrinkage, or burn marks.
Optimizing Product Design
Mold flow analysis enables engineers to refine part geometries for improved manufacturability. By visualizing how PVC flows through the mold, potential problem areas such as thin walls, sharp corners, or intricate features can be redesigned to ensure uniform filling and reduce the risk of defects like voids or weld lines.
Tooling and Mold Design Enhancement
For PVC products, mold design is crucial to achieving dimensional accuracy and surface finish. Mold flow analysis provides valuable data to optimize gate locations, runner systems, and cooling channels. This prevents issues like uneven cooling or air entrapment, ensuring consistent product quality and reducing cycle times.
Reducing Defects and Improving Efficiency
By predicting potential manufacturing challenges, mold flow analysis allows manufacturers to address problems proactively. For example, it can identify areas prone to high stress or improper filling, enabling adjustments to the mold or process. This results in fewer production errors, less material waste, and increased efficiency in mass production.