The automotive industry has seen rapid advancements in technology and design, with dashboards evolving into complex, high-tech interfaces that integrate digital displays, touchscreens, and a variety of user-focused components. To produce these advanced dashboard components, manufacturers rely heavily on injection molding techniques to create precision parts that meet both aesthetic and functional requirements. In this article, we will explore the trends and challenges associated with molds for dashboard components.
Trends in Molds for Dashboard Components
Integration of Multi-Material Molding Modern dashboards incorporate multiple materials for different functional areas, from soft-touch surfaces to hard, durable plastic components. Manufacturers are adopting multi-material injection molding, which allows for the combination of soft and hard plastics in a single mold. This results in more intricate designs, improved ergonomics, and better cost efficiency. These multi-material molds often utilize insert molding techniques, where a preformed material is placed in the mold before injection of the secondary material.
Customization for Aesthetic Designs With the rise of vehicle personalization, automakers are increasingly focused on customizing the dashboard experience. The demand for unique textures, colors, and finishes on dashboard components has pushed mold manufacturers to develop innovative techniques, such as 3D printing of molds and advanced surface treatment technologies. These methods allow for the creation of dashboards with customized textures, intricate patterns, and even wood or metal-like appearances.
Lightweight Materials Reducing the overall weight of a vehicle is a key trend in the automotive industry, not only for performance but also to improve fuel efficiency. The use of lightweight, durable materials such as high-strength thermoplastics, composites, and advanced polymers in dashboard molding has been growing. These materials offer the same strength and durability while reducing weight, and they allow for more cost-effective production. The challenge lies in designing molds that can handle the unique properties of these lightweight materials.
Smart and Digital Components Integration Dashboards are increasingly becoming hubs of smart technology, incorporating digital displays, touchscreens, and even augmented reality systems. Molds for dashboard components must be able to accommodate these advanced technologies, which means precise, high-quality molds capable of ensuring the smooth functioning of sensitive electronics. Mold manufacturers must also consider the need for provisions for cable routing, heat dissipation, and moisture protection.
Sustainability and Eco-friendly Molding Solutions Environmental consciousness has become a central theme across industries, and the automotive sector is no exception. There is a growing emphasis on sustainability, with automakers pushing for the use of recyclable materials and reducing the environmental impact of manufacturing processes. Molds for dashboard components are being designed with sustainability in mind, using recyclable thermoplastics, bio-based materials, and energy-efficient molding techniques to reduce waste and carbon footprints.
Challenges in Molds for Dashboard Components
Complex Geometries and Tight Tolerances One of the key challenges in molding dashboard components is the intricate, often complex designs that manufacturers require. Modern dashboards include curved, multi-faceted surfaces, often with integrated screen cutouts, air vents, and switch assemblies. Creating molds that can produce these complex geometries while maintaining tight tolerances can be difficult and costly. The challenge lies in ensuring that the molds can consistently produce high-quality parts that meet stringent automotive standards for both functionality and aesthetics.
Material Compatibility and Performance As dashboard components incorporate a variety of materials—such as soft-touch surfaces, hard plastics, and composites—it is essential to ensure that the mold design accommodates the thermal expansion and contraction properties of each material. Achieving optimal material compatibility while avoiding issues like warping, cracking, or poor adhesion between layers requires sophisticated mold design and a careful selection of materials. The challenge is even more pronounced when integrating electronics, which require mold designs that can handle issues like heat dissipation and electromagnetic shielding.
Mold Wear and Durability Injection molds for dashboard components are subjected to high pressures and temperatures during the production process, leading to wear and tear over time. For high-volume production runs, molds must be extremely durable to avoid degradation, which can impact the overall quality of the parts. Mold manufacturers face the challenge of creating long-lasting molds that can withstand repeated cycles of high-stress injection molding without compromising the final product’s precision or finish.
Tooling Costs and Lead Times Tooling for automotive dashboard components is typically costly and time-consuming to develop. The design and fabrication of complex molds require advanced technology, skilled labor, and significant investment. Furthermore, lead times for mold production can range from several weeks to months, depending on the complexity of the design. As a result, manufacturers must carefully balance the need for custom, high-quality molds with the associated costs and timelines.
Quality Control and Consistency Ensuring that each dashboard component produced meets the high standards of quality and consistency is a significant challenge. With the increasing complexity of molds and the variety of materials used, it becomes more difficult to maintain uniformity across production runs. This is especially critical in the automotive industry, where dashboard components not only need to be visually appealing but also functional, with features such as accurate fitment for control panels, precise alignment with sensors, and reliable durability over time.
Conclusion
Molding for dashboard components is an intricate process that requires advanced technology, precision, and an understanding of automotive design trends. While there are many exciting developments, such as multi-material molding and the integration of digital components, manufacturers face several challenges, including complex geometries, material compatibility, tooling costs, and maintaining high standards of quality control. As dashboard technology continues to evolve, mold manufacturers will need to stay ahead of these trends and challenges to deliver innovative, high-quality solutions for the automotive industry.
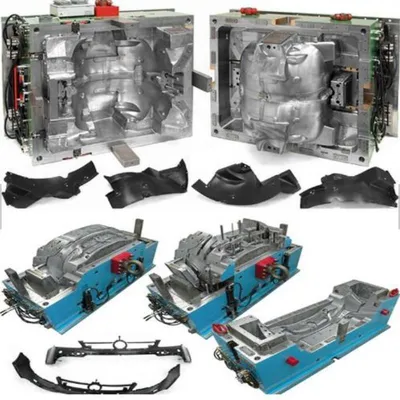