The automotive industry is rapidly evolving, driven by the demand for lightweight, fuel-efficient, and high-performance vehicles. As part of this transformation, the materials used in manufacturing molds—critical components in forming and shaping automotive parts—are also undergoing significant innovation. Next-generation automotive mold materials are designed to enhance performance, reduce costs, and meet stringent sustainability and regulatory standards.
1. Drivers for Innovation in Mold Materials
Lightweighting initiatives: The shift towards lighter vehicle structures has increased the use of advanced plastics and composites, necessitating molds that can withstand new material behaviors.
EV and Hybrid growth: Electric and hybrid vehicles require precision components, often with complex geometries, demanding superior mold accuracy and durability.
Sustainability goals: There is a push for recyclable mold materials and more energy-efficient molding processes.
High-volume production demands: Modern molds must endure millions of cycles with minimal wear, especially for high-throughput production lines.
2. Types of Next-Generation Mold Materials
a. Advanced Tool Steels
Characteristics: High hardness, excellent wear resistance, thermal conductivity, and dimensional stability.
Examples: H13 with enhanced alloying, or maraging steels like 18Ni300.
Applications: Injection molds for structural parts, interior trim components, and under-the-hood parts.
b. Beryllium-Copper Alloys
Characteristics: Exceptional thermal conductivity, moderate strength, good corrosion resistance.
Use Case: Ideal for inserts in molds where rapid cooling is required (e.g., for lenses or optical components).
Drawback: Cost and health concerns during machining.
c. Aluminum Alloys
Characteristics: Lightweight, high thermal conductivity, good machinability.
Advantage: Faster cycle times due to superior heat dissipation.
Limitation: Lower durability compared to steel in high-pressure applications.
d. Nickel-Based Superalloys
Characteristics: Outstanding heat resistance and corrosion protection.
Applications: Molds for high-temperature thermoplastics and composites.
e. Composite and Hybrid Mold Materials
Example: Ceramic-metal matrix composites (CMMCs), carbon fiber-reinforced molds.
Advantage: Combines thermal and mechanical benefits of multiple materials.
Future Potential: Customizable for specific applications in additive manufacturing.
3. Emerging Trends and Technologies
Additive Manufacturing (AM) of Molds
Enables conformal cooling channels, reducing cycle times and improving part quality.
Allows for lightweight mold structures with optimized performance.
Materials include tool steel powders, ceramic-infused resins, and hybrid polymers.
Surface Treatments and Coatings
PVD, nitriding, and DLC coatings increase surface hardness, reduce friction, and extend mold life.
Self-lubricating coatings for high-cavity or complex molds are gaining traction.
Smart Mold Materials
Integration of sensors into mold materials for real-time monitoring (temperature, pressure, wear).
Supports predictive maintenance and quality control.
4. Sustainability and Recycling Considerations
Recyclable mold base materials and eco-friendly coatings are becoming standard.
Life-cycle assessments (LCA) guide the selection of mold materials with the lowest environmental impact.
Water- and solvent-free mold release technologies reduce chemical use during production.
5. Conclusion
Next-generation automotive mold materials are pivotal to the industry’s transformation toward more sustainable, efficient, and high-performance manufacturing. By leveraging advanced metals, composites, and additive processes, automakers and suppliers can achieve better part quality, lower costs, and shorter development cycles. As innovation continues, the integration of smart features and sustainability metrics will further shape the mold materials landscape.
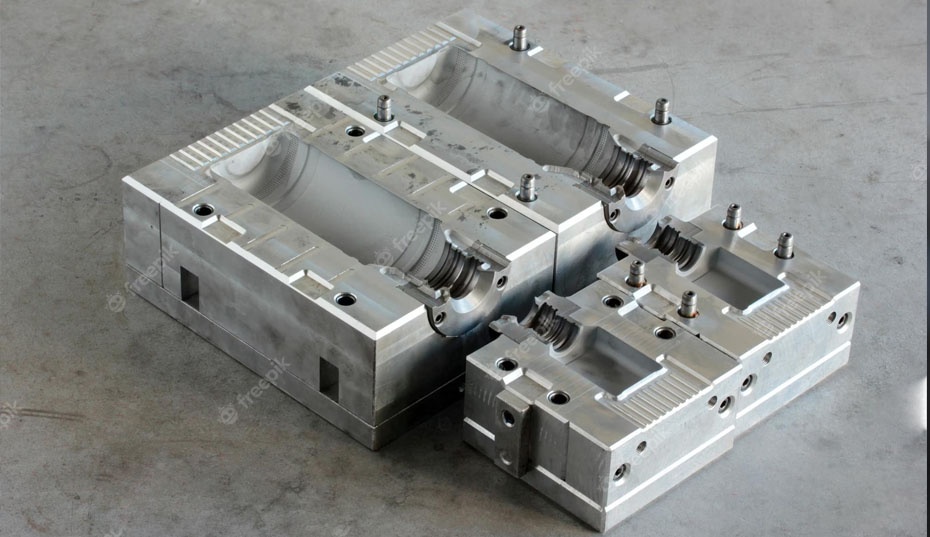