Precision molding plays a critical role in the modern automotive industry. As vehicles become more advanced, the need for highly accurate, durable, and lightweight components has increased. Precision molding offers a manufacturing solution that meets stringent quality and performance standards, making it indispensable in producing complex automotive parts.
What is Precision Molding?
Precision molding is a manufacturing process that involves shaping plastic or metal materials into highly detailed and accurate parts using custom-designed molds. This process ensures that the final products have exact dimensions, tight tolerances, and consistent quality, which are vital in automotive applications.
Key Applications in the Automotive Industry
Engine Components: Precision-molded parts such as valve covers, intake manifolds, and sensor housings are essential for high-performance engines.
Interior Parts: Dashboards, door panels, and air vents require tight tolerances for aesthetic and functional integrity.
Lighting Systems: Headlight and taillight housings are often made through precision molding to ensure proper fit and optical clarity.
Electronic Housings: Control modules, connectors, and sensor casings are produced with precision to protect sensitive electronics.
Safety Components: Airbag housings, seat belt mechanisms, and other critical safety parts rely on the consistency of precision molding.
Advantages of Precision Molding in Automotive Manufacturing
High Dimensional Accuracy: Ensures components fit together seamlessly, reducing the risk of failure.
Enhanced Durability: Produces parts with excellent mechanical properties suitable for harsh automotive environments.
Cost Efficiency at Scale: Once molds are developed, large production runs are economical and consistent.
Weight Reduction: Lightweight plastic composites replace heavier metal parts, improving fuel efficiency.
Customization and Complexity: Allows for intricate geometries and custom features that would be difficult or impossible with traditional methods.
Materials Used
Thermoplastics: Such as ABS, polycarbonate, and nylon, used for components requiring high strength and flexibility.
Thermosetting Plastics: Ideal for high-heat or structural applications.
Metal Injection Molding (MIM): Used for smaller metal parts with complex shapes, such as gears and fasteners.
Technological Innovations
Multi-shot Molding: Combines different materials or colors in a single molding cycle.
Insert Molding: Integrates metal inserts into plastic parts during molding.
Overmolding: Allows layering of materials to enhance functionality or comfort, such as rubberized grips.
Automation and Robotics: Increases precision, repeatability, and production speed.
Challenges and Considerations
Tooling Costs: Initial mold creation is expensive and time-consuming.
Material Selection: Requires careful consideration of temperature resistance, strength, and compatibility.
Quality Control: Maintaining tight tolerances demands rigorous inspection and process control.
Environmental Concerns: Emphasis on recyclable materials and sustainable practices is growing.
Future Outlook
As vehicles continue to evolve toward electrification and autonomy, the demand for lightweight, high-performance, precision-molded components will grow. Innovations in material science and automation are expected to further improve the capabilities and applications of precision molding in the automotive sector.
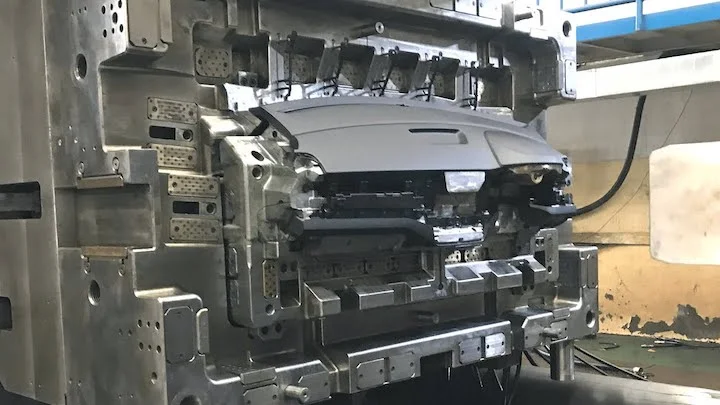