PVC molding machines are crucial assets in industries such as automotive, construction, and consumer goods, where polyvinyl chloride (PVC) components are manufactured. Ensuring these machines operate efficiently with minimal downtime is critical for productivity and profitability. Predictive maintenance (PdM) offers a modern, data-driven approach to equipment upkeep, going beyond traditional preventive maintenance by anticipating failures before they occur.
What is Predictive Maintenance?
Predictive maintenance uses real-time data, sensors, machine learning, and analytics to monitor the condition of equipment and predict potential failures. This strategy enables maintenance teams to perform interventions only when necessary, reducing unplanned downtime and maintenance costs.
Why PVC Molding Machines Need Predictive Maintenance
PVC molding machines often operate in high-temperature and high-pressure environments, processing thermoplastic materials with precise tolerances. Common issues include:
Wear of injection screws and barrels
Hydraulic system degradation
Heater band failures
Electrical motor faults
Mold alignment issues
Early detection of these problems is critical to avoid costly machine failures or product defects.
Key Components for Implementing Predictive Maintenance
Sensors and IoT Devices
Temperature sensors
Vibration sensors
Pressure transducers
Flow meters
Current and voltage monitors
Data Collection and Integration
Real-time data acquisition from machine PLCs (Programmable Logic Controllers)
Integration with MES (Manufacturing Execution Systems) or cloud platforms
Data Analytics and Machine Learning
Pattern recognition and anomaly detection
Remaining useful life (RUL) predictions
Trend analysis for early fault detection
Alert and Notification Systems
Automated alerts via SMS, email, or maintenance dashboards
Maintenance scheduling based on predictive models
Benefits of Predictive Maintenance for PVC Molding Machines
Reduced Downtime: Prevents unexpected equipment failures and minimizes production halts.
Cost Savings: Reduces unnecessary maintenance and spare parts inventory.
Extended Equipment Life: Timely maintenance prevents accelerated wear and tear.
Improved Product Quality: Minimizes production defects caused by suboptimal machine conditions.
Safety Enhancements: Detects potential hazards before they become critical.
Challenges and Considerations
Initial Investment: Cost of sensors, data platforms, and training.
Data Management: Handling and interpreting large volumes of data.
Integration Complexity: Compatibility with existing machinery and control systems.
Skilled Personnel: Requires expertise in data analytics, maintenance, and operations.
Case Example
A PVC pipe manufacturing plant implemented predictive maintenance by installing vibration and temperature sensors on critical molding machines. Using machine learning models, they detected bearing wear in hydraulic pumps two weeks before failure. This allowed for scheduled maintenance, saving thousands in downtime and repair costs.
Conclusion
Predictive maintenance transforms the maintenance strategy for PVC molding machines from reactive to proactive. By leveraging sensor data and analytics, manufacturers can boost machine reliability, ensure consistent product quality, and achieve significant cost savings. As Industry 4.0 technologies become more accessible, predictive maintenance is rapidly becoming a standard best practice in plastic manufacturing.
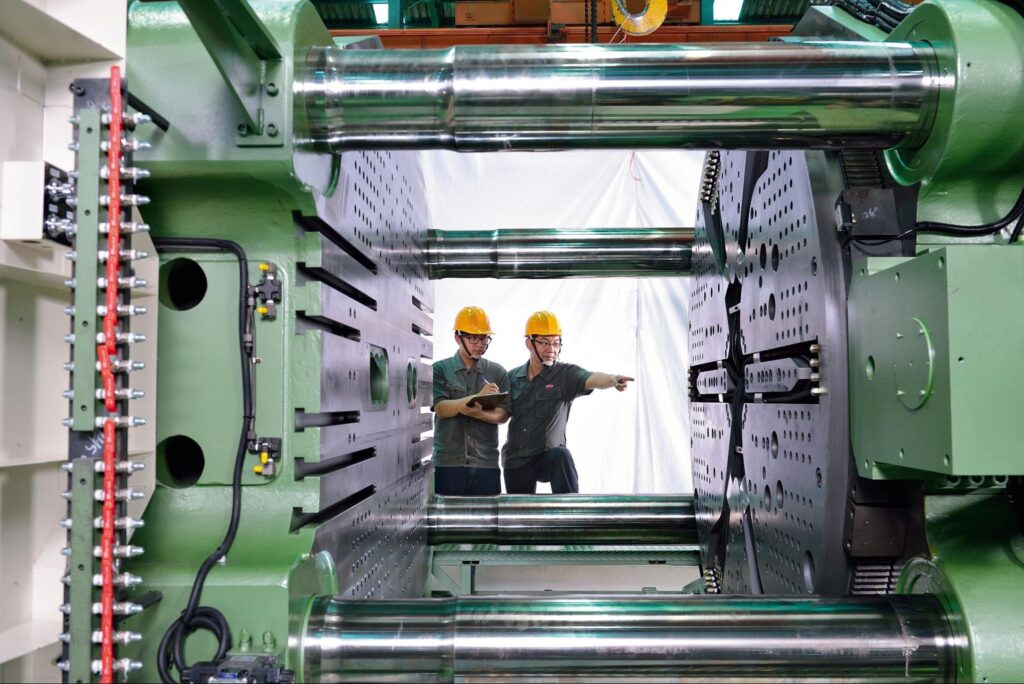