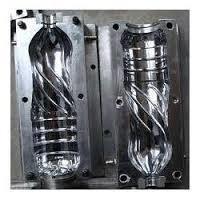
Polyvinyl chloride (PVC) blow molding is a manufacturing process used to create durable and customizable bottles for a wide range of industries. Known for its strength, versatility, and affordability, PVC is an ideal material for producing bottles used in food and beverage, pharmaceuticals, personal care, and industrial applications. The process involves heating and shaping PVC to produce lightweight and robust containers tailored to specific requirements.
PVC bottles are manufactured using three primary blow molding techniques: extrusion blow molding, injection blow molding, and stretch blow molding. In extrusion blow molding, a molten PVC tube, called a parison, is extruded and inflated with compressed air to take the shape of a mold. Injection blow molding begins with forming a pre-shaped parison using injection molding, which is then reheated and expanded in a blow mold. Stretch blow molding, typically used for lightweight and high-strength bottles, stretches the material axially and radially to enhance strength and improve material distribution.
The benefits of PVC in blow molding are numerous. PVC’s inherent durability ensures that bottles can withstand impacts and resist damage during transportation and handling. Its excellent chemical resistance makes it suitable for storing reactive substances like detergents and industrial chemicals. PVC can also be formulated for clarity, offering transparent bottles that allow the contents to be visible, which is advantageous for food, beverages, and cosmetic products. Additionally, PVC bottles can be easily colored or shaped, providing design flexibility for branding and functionality.
Achieving high-quality results with PVC blow molding requires precise control of process parameters. Maintaining the correct temperature range (160–210°C) prevents material degradation while ensuring optimal flow. Consistent air pressure and adequate cooling times are critical for achieving uniform wall thickness and preventing defects such as shrinkage or warping. Additives like stabilizers and lubricants are often used to enhance PVC’s processability and improve the surface finish of the bottles.
PVC bottles find applications in various industries. In the food and beverage sector, they are commonly used for packaging edible oils, sauces, and juices. The pharmaceutical industry relies on PVC bottles for syrups and medicinal liquids, while personal care products such as shampoos and lotions are frequently packaged in PVC containers. Additionally, PVC bottles are widely used for storing industrial chemicals, thanks to their resistance to harsh substances.
While PVC blow molding offers numerous advantages, challenges remain. Environmental concerns related to PVC production, such as the use of chlorine and phthalates, have prompted manufacturers to adopt bio-based and phthalate-free formulations. Advances in temperature control systems and process optimization also help mitigate issues like material degradation during production. Furthermore, PVC bottles are recyclable, aligning with growing demands for sustainable packaging solutions.