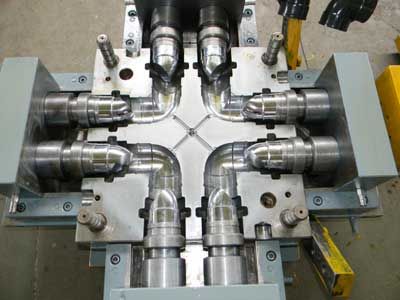
Polyvinyl chloride (PVC) is one of the most versatile thermoplastics used in molding and manufacturing, known for its durability, affordability, and adaptability. It plays a vital role in industries ranging from construction to consumer goods, owing to its ability to be customized for strength, flexibility, and appearance. Its suitability for various molding techniques has made PVC a cornerstone of modern manufacturing.
Characteristics of PVC
- Durability: Resistant to impact, weather, chemicals, and abrasion, making it ideal for long-lasting applications.
- Versatility: Available in rigid and flexible forms, accommodating a wide range of product requirements.
- Low Cost: Economical compared to other plastics, while maintaining excellent performance characteristics.
- Chemical Resistance: Resistant to acids, bases, and many chemicals, ideal for industrial and domestic use.
- Ease of Processing: Suitable for multiple molding methods, including injection, extrusion, blow, and compression molding.
Molding Techniques for PVC
Injection Molding
- Used for producing intricate and high-precision parts, such as electrical fittings, plumbing components, and toys.
- Process involves melting PVC granules and injecting them into a mold cavity to form the desired shape.
Blow Molding
- Ideal for hollow parts like bottles, containers, and storage tanks.
- The process involves inflating a molten PVC parison within a mold to create hollow forms.
Extrusion Molding
- Commonly used for continuous shapes like pipes, window frames, and siding.
- PVC is melted and pushed through a die to form a continuous profile, then cooled and cut to length.
Compression Molding
- Utilized for larger, simple parts like panels, mats, and tiles.
- Heated PVC is compressed in a mold to take its shape.
Calendering
- Produces PVC sheets and films for use in flooring, wall coverings, and signage.
Applications of PVC in Manufacturing
Construction
- Pipes and Fittings: Widely used in plumbing and irrigation systems due to its strength and corrosion resistance.
- Windows and Doors: Rigid PVC provides excellent insulation and durability.
- Flooring: Flexible PVC is used in tiles and sheets for its ease of maintenance and variety of designs.
Automotive
- Interior Components: Dashboards, door panels, and seat coverings leverage PVC’s durability and design flexibility.
- Cable Insulation: Flexible PVC is preferred for its thermal and electrical insulating properties.
Medical
- Tubes and Bags: Used for medical-grade applications like IV bags and tubing due to its non-toxic formulations and sterilizability.
Consumer Goods
- Household Items: Toys, furniture, and appliances benefit from PVC’s cost-effectiveness and customization.
- Packaging: Bottles, blister packs, and films are made using PVC for its transparency and strength.
Electrical
- Cable Coating: Ensures safe insulation for electrical wiring.
- Switches and Sockets: Combines electrical resistance with durability.
Advantages of PVC in Molding and Manufacturing
- Customizability: PVC can be modified with additives to achieve desired properties like color, flexibility, or UV resistance.
- Eco-Friendly Options: Recyclable PVC grades and bio-based alternatives are increasingly available, reducing environmental impact.
- Lightweight: Combines low weight with high strength, making it easier to handle and transport.
- Weather Resistance: Performs well in outdoor applications due to its resistance to moisture and UV radiation.
- Fire Retardancy: Some PVC formulations are inherently flame-resistant, adding safety for specific applications.
Challenges in Using PVC
Environmental Concerns
- Traditional PVC production involves chlorine, raising concerns about environmental impact.
- Solution: Manufacturers are shifting to sustainable production practices and recycling initiatives.
Processing Sensitivity
- PVC requires precise temperature control to avoid degradation during processing.
- Solution: Modern equipment and formulations help manage this challenge effectively.
Brittleness at Low Temperatures
- Rigid PVC can become brittle in extreme cold.
- Solution: Plasticizers are added to improve flexibility for applications in colder climates.
Future Trends in PVC Manufacturing
Bio-Based PVC
- Innovations in bio-based and phthalate-free PVC formulations aim to reduce reliance on fossil fuels and improve environmental sustainability.
Advanced Recycling
- Mechanical and chemical recycling methods are enhancing the reusability of PVC, making it more eco-friendly.
Smart Materials
- Integration of conductive or antimicrobial properties into PVC expands its applications in electronics and healthcare.
Lightweight Composites
- PVC combined with other materials like fiberglass offers enhanced strength-to-weight ratios for automotive and construction use.