Polyvinyl chloride (PVC) has long been a staple material in the medical device industry due to its flexibility, chemical stability, biocompatibility, and cost-effectiveness. Recent innovations in PVC molding technologies are further revolutionizing medical device manufacturing, enabling higher precision, enhanced safety, and better performance across a wide array of medical applications.
Why PVC Remains a Cornerstone Material
PVC is highly valued in the medical field for several key reasons:
Biocompatibility: Suitable for direct contact with bodily fluids and tissues.
Sterilizability: Can withstand common sterilization methods such as ethylene oxide (EtO), gamma radiation, and steam autoclaving.
Flexibility and Clarity: Offers the physical characteristics needed for devices like tubing, blood bags, catheters, and IV components.
Cost-efficiency: Low production cost relative to alternatives like silicone and thermoplastic elastomers (TPEs).
Key Innovations in PVC Molding Technologies
1. Micro-Molding for Miniaturized Devices
Advancements in micro-molding techniques now allow manufacturers to produce highly precise miniature components with tight tolerances. This is critical for devices such as:
Microcatheters
Intravenous connectors
Implantable devices
Micro-molding of PVC is particularly challenging due to its thermal sensitivity, but modern process controls and tooling innovations have made it feasible and reliable.
2. Overmolding and Multi-Material Integration
Overmolding PVC with other polymers enables the creation of complex, multi-functional components. For instance:
Soft-touch grips on surgical tools
Integrated seals or valves
Composite connectors combining rigid and flexible segments
This capability enhances usability, ergonomics, and device performance, especially in handheld or wearable devices.
3. Precision Extrusion and Blow Molding
Innovations in extrusion and blow molding techniques have improved consistency and wall thickness control for PVC tubing and fluid bags. High-precision blow molding is now used to form custom-shaped containers and chambers for diagnostic and infusion applications.
4. Environmentally Safer Plasticizers
Traditional PVC formulations often relied on phthalate-based plasticizers (like DEHP), which have raised health and environmental concerns. New formulations using safer, bio-based plasticizers (such as DOTP or TOTM) offer the same flexibility without toxicological risks, making them ideal for neonatal and dialysis applications.
5. Advanced Tooling and Automation
CNC-machined molds and smart manufacturing platforms now support greater automation in PVC molding, reducing human error and enhancing repeatability. Real-time process monitoring ensures consistent part quality and regulatory compliance—a key requirement in FDA-regulated environments.
Applications Benefiting from These Innovations
IV Systems and Blood Bags: Enhanced durability and transparency for fluid visibility.
Catheters and Tubing: More accurate sizing and smoother surfaces to reduce patient trauma.
Diagnostic Devices: Integration of microchannels and chambers for point-of-care testing.
Wearable Drug Delivery Systems: Soft, flexible housings with embedded sensors.
Regulatory and Sustainability Considerations
Innovations must align with regulatory standards such as ISO 10993 for biocompatibility and FDA 21 CFR for medical-grade materials. Additionally, sustainable PVC alternatives and recycling initiatives are gaining attention, addressing environmental concerns associated with single-use medical plastics.
Conclusion
PVC molding innovations are driving significant progress in medical device manufacturing, making products safer, more effective, and more tailored to patient needs. As material science and process engineering continue to evolve, PVC will likely maintain its pivotal role—especially as more sustainable, high-performance formulations emerge.
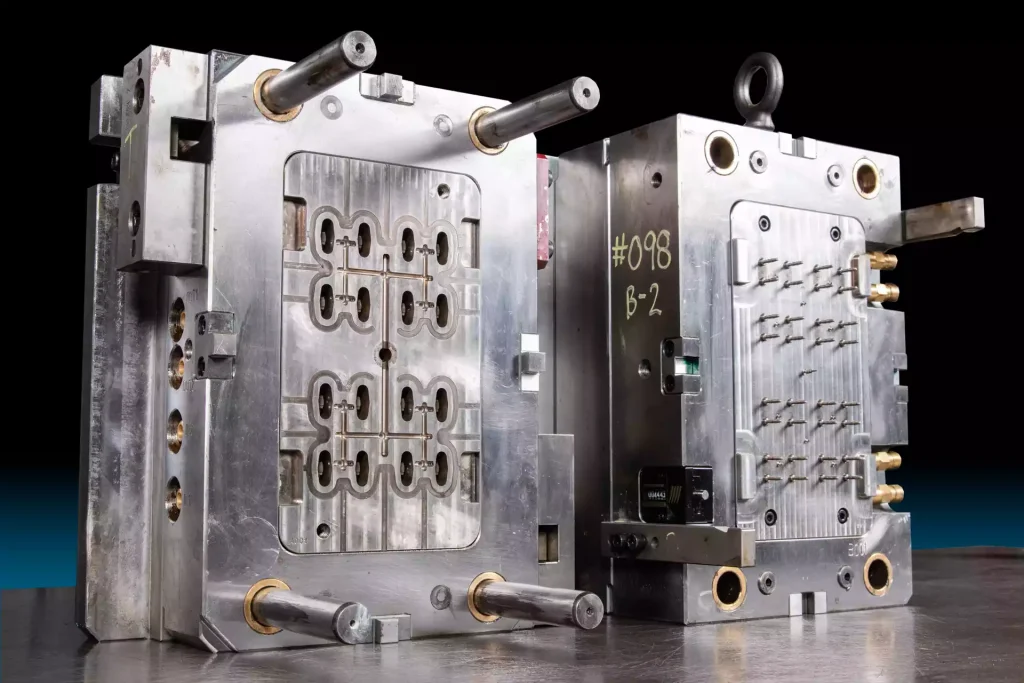