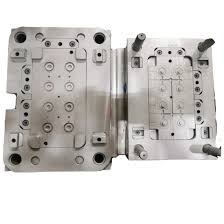
Polyvinyl chloride (PVC) is a versatile material widely used in the automotive industry, particularly for creating molds that produce high-quality components. Its unique combination of durability, flexibility, and cost-efficiency makes it an excellent choice for manufacturing a range of automotive parts, such as interior panels, seals, wiring insulation, and protective covers.
One of the key advantages of PVC in mold production is its exceptional resistance to wear, corrosion, and environmental factors such as heat, moisture, and UV radiation. These properties ensure that automotive components maintain their performance and appearance even under demanding conditions. Additionally, PVC’s flexibility allows it to accommodate intricate designs, enabling the creation of detailed and customized parts that meet specific functional and aesthetic requirements.
PVC molds also contribute to sustainability in automotive manufacturing. The material is recyclable, and its ability to withstand multiple production cycles without degrading ensures long-lasting performance and reduced material waste. Moreover, PVC’s compatibility with advanced molding techniques, such as injection molding and compression molding, allows for efficient and high-volume production with consistent quality.
From a cost perspective, PVC molds are an economical solution for automotive component manufacturing. They offer a balance between affordability and performance, making them suitable for both standard and specialized applications. Furthermore, the material’s ability to be modified with additives enhances its properties, such as increased fire resistance, thermal stability, or improved flexibility, ensuring versatility across diverse automotive needs.