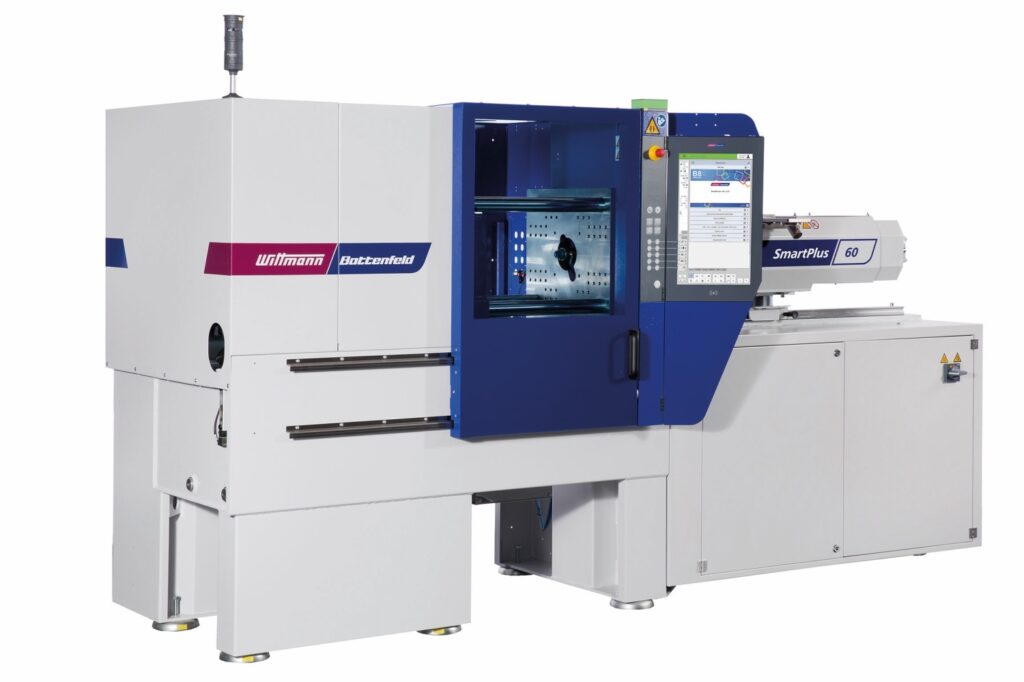
Smart injection molding technologies are transforming the manufacturing industry by integrating automation, artificial intelligence (AI), real-time data analytics, and IoT (Internet of Things) to enhance efficiency, precision, and sustainability. These advancements allow manufacturers to reduce waste, optimize energy consumption, and improve quality control, making the injection molding process more cost-effective and adaptable to complex production requirements.
Key Innovations in Smart Injection Molding
1. Industry 4.0 and IoT Integration
Smart injection molding systems leverage IoT sensors and cloud-based connectivity to enable real-time monitoring of critical parameters such as temperature, pressure, and injection speed. These connected machines allow manufacturers to:
- Detect and correct defects in real-time, reducing scrap rates.
- Remotely monitor production lines for improved operational efficiency.
- Use predictive maintenance to prevent unexpected machine failures, reducing downtime.
2. AI-Driven Process Optimization
Artificial intelligence and machine learning algorithms analyze vast amounts of production data to enhance process stability and consistency. AI-powered molding systems can:
- Automatically adjust parameters (such as injection speed and pressure) to compensate for material variations.
- Predict defects before they occur, ensuring high-quality molded components.
- Optimize cycle times and energy consumption for greater efficiency.
3. Automation and Robotics
Modern injection molding facilities utilize collaborative robots (cobots) and automated systems to streamline production processes. These robots assist in:
- Material handling and feeding, ensuring consistent resin flow.
- Part removal and assembly, reducing manual labor costs and increasing precision.
- In-line quality inspection, ensuring defect-free products without slowing down production.
4. Smart Molds with Embedded Sensors
Next-generation molds are equipped with embedded sensors that monitor conditions inside the mold cavity. These smart molds help manufacturers:
- Detect pressure imbalances or cooling inefficiencies, preventing defects like warping or sink marks.
- Ensure consistent part quality by adjusting parameters automatically.
- Improve mold lifespan by identifying wear and tear in advance.
5. Energy-Efficient and Sustainable Molding
Smart injection molding technologies focus on reducing energy consumption and waste through:
- Servo-driven electric injection molding machines, which use up to 70% less energy than hydraulic systems.
- Advanced cooling and heat recovery systems, optimizing thermal management.
- Recyclable and biodegradable material integration, reducing environmental impact.
6. Digital Twin Technology for Simulation
Manufacturers use digital twins—virtual models of the injection molding process—to simulate and optimize production parameters before actual manufacturing. This allows:
- Faster design validation and fewer trial-and-error iterations.
- Improved material flow analysis, reducing defects.
- Enhanced product customization with minimal downtime.
The Future of Smart Injection Molding
As AI, automation, and IoT technologies continue to advance, the injection molding industry is moving toward fully autonomous production lines. Future trends include:
- Self-learning molding systems that continuously improve performance.
- 5G-enabled smart factories for ultra-fast data transmission.
- Blockchain technology for supply chain transparency and traceability.