Automotive molding, which includes the manufacture of components such as bumpers, trims, dashboards, and sealing systems, plays a crucial role in vehicle aesthetics, safety, and performance. To ensure consistent quality, safety, and interoperability, automotive molding processes and products must adhere to a variety of international standards and certifications.
1. Importance of Standards and Certifications
Quality Assurance: Standards ensure consistent product quality across manufacturers.
Safety Compliance: Certification helps meet legal and safety requirements.
Supply Chain Uniformity: Enables compatibility and standardization across global supply chains.
Market Access: Certification is often a prerequisite to enter certain international markets.
2. Key Standards in Automotive Molding
a. ISO 9001 – Quality Management Systems
Applies to any manufacturing organization.
Focuses on quality assurance and continuous improvement.
Ensures consistency in production processes, including molding.
b. IATF 16949 – Automotive Quality Management
Specific to the automotive sector.
Based on ISO 9001 with additional automotive-specific requirements.
Focuses on defect prevention, variation reduction, and waste in the supply chain.
c. ISO 14001 – Environmental Management Systems
Helps manufacturers manage environmental responsibilities.
Relevant for sustainable practices in material selection and waste reduction in molding.
d. ISO 45001 – Occupational Health & Safety
Ensures safe working conditions in production environments, including molding facilities.
3. Material and Product-Specific Standards
a. ASTM Standards
Widely used in the U.S. for testing materials like plastics and elastomers.
Examples:
ASTM D638 – Tensile properties of plastics.
ASTM D790 – Flexural properties of plastics.
ASTM D256 – Impact resistance of plastics.
b. SAE Standards (Society of Automotive Engineers)
Commonly used in North America for automotive engineering.
Includes material specifications, testing procedures, and part performance.
Examples:
SAE J200 – Classification of rubber materials.
SAE J400 – Chip resistance of coatings.
c. UL Standards (Underwriters Laboratories)
Especially for molded parts with electrical or flammability considerations.
Example: UL 94 – Flammability testing for plastic materials.
4. Industry and OEM-Specific Certifications
OEM Requirements: Major automakers (e.g., Toyota, BMW, Ford) often impose proprietary standards on top of international norms.
PPAP (Production Part Approval Process): A requirement for suppliers to demonstrate part readiness, especially in injection molding.
IMDS (International Material Data System): A database used by automotive OEMs to track material compositions for compliance with environmental regulations like REACH and ELV.
5. Testing and Validation
To meet these standards, various mechanical, chemical, and environmental tests are conducted, including:
Tensile, flexural, and impact tests.
Heat aging and UV resistance tests.
Dimensional stability and surface finish assessments.
Fatigue and vibration analysis.
6. Certification Bodies
TÜV Rheinland
SGS
Bureau Veritas
Intertek
UL Solutions
These third-party organizations audit and certify compliance with relevant standards.
Conclusion
Standards and certifications in automotive molding ensure that the components meet rigorous requirements for performance, safety, and environmental compliance. Adhering to them is critical for manufacturers seeking quality assurance, customer trust, and access to global markets.
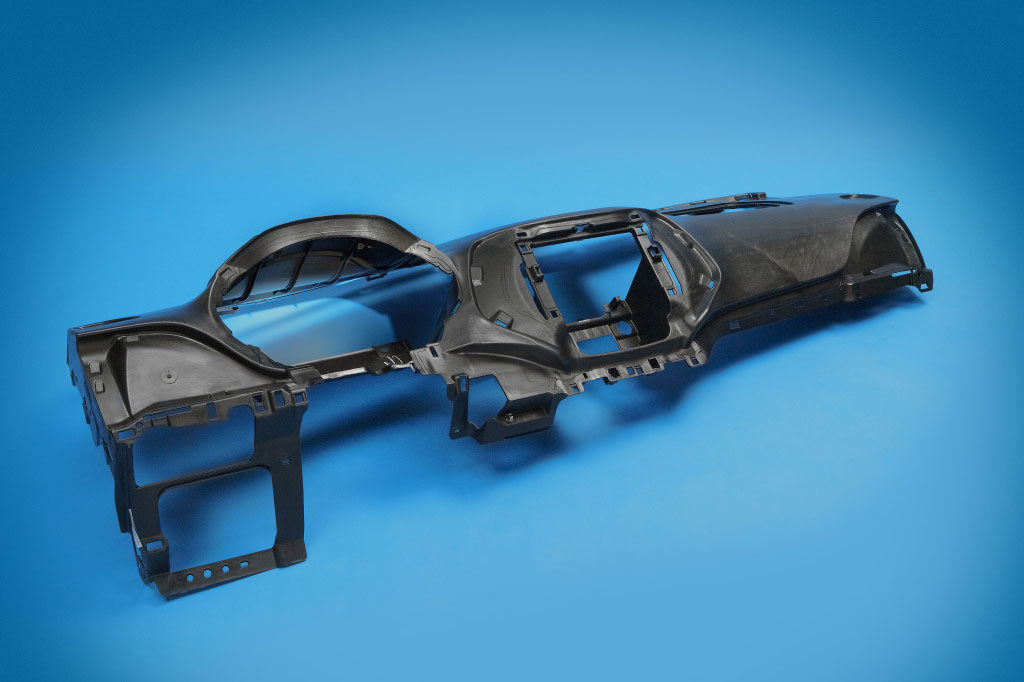