Injection molding is a widely used manufacturing process for producing a variety of parts, from small plastic components to large automotive or industrial pieces. As industries continue to evolve, automation has become a central player in transforming injection molding, increasing efficiency, precision, and cost-effectiveness. In this context, automation refers to the use of advanced machinery, robotics, and computer systems to carry out processes traditionally handled by humans.
Here’s a detailed look at the role of automation in modern injection molding:
1. Enhanced Precision and Quality Control
Automation significantly improves the precision of injection molding processes. Robots and automated systems can perform tasks like part handling, assembly, and quality inspection with extremely high accuracy. For instance, automated vision systems can check for defects or inconsistencies in molded parts, ensuring only high-quality products are produced. These systems reduce human error, leading to more uniform and reliable parts.
2. Increased Production Speed
Automated systems can operate much faster than manual processes. Robots can carry out repetitive tasks such as inserting components, extracting molded parts, and performing secondary operations at high speeds. These systems do not require breaks or downtime, making them more efficient than human labor. In addition, automation allows for faster cycle times, reducing overall production times and increasing output, which is especially important in industries with high-demand and high-volume requirements.
3. Cost Efficiency
While the initial investment in automated systems can be high, over time, automation leads to significant cost savings. It reduces the need for manual labor, minimizes material waste, and cuts down on production errors, all of which contribute to reducing costs. Additionally, automation can allow manufacturers to run production lines 24/7, increasing overall output without needing to hire more workers for overnight or weekend shifts.
4. Complex Part Handling and Customization
Automation can handle a wide variety of tasks in injection molding that would be difficult or impossible to perform manually. Robots equipped with advanced grippers and sensors can handle complex parts with intricate shapes or fragile materials. Additionally, automated systems allow for the integration of more sophisticated features, such as multi-material injection molding or custom molding cycles for specialized product designs. These systems provide manufacturers with the flexibility to produce a wide range of products without the need for extensive manual intervention.
5. Data Collection and Monitoring
One of the significant benefits of automation in injection molding is the ability to collect real-time data. Automated systems are typically connected to central databases, where production data, such as temperature, pressure, and cycle time, is recorded continuously. This data allows manufacturers to monitor the health of machines, predict maintenance needs, and make real-time adjustments to ensure optimal performance. The ability to analyze this data also aids in troubleshooting, further enhancing production efficiency and reducing downtime.
6. Integration with Industry 4.0
As part of the broader Industry 4.0 trend, automated injection molding systems are increasingly incorporating advanced technologies like the Internet of Things (IoT), artificial intelligence (AI), and machine learning. IoT sensors can communicate machine performance and production status to operators, while AI algorithms can predict potential failures and suggest adjustments to optimize processes. This interconnectedness leads to smarter factories and more autonomous production environments.
7. Safety Improvements
Automation in injection molding enhances safety by reducing the need for human workers to interact directly with machines during critical processes. Robots can take over dangerous or high-risk tasks, such as handling molten materials or working in high-temperature environments. This minimizes the risk of injury, ensuring a safer working environment for employees.
8. Sustainability
Automation also plays a role in making injection molding more environmentally sustainable. Automated systems reduce material waste by providing precise control over the injection process, ensuring that only the necessary amount of material is used. Additionally, automated systems can optimize energy use by adjusting the temperature and pressure settings according to real-time conditions. This can lead to lower energy consumption and reduced environmental impact.
Conclusion
The integration of automation in modern injection molding has revolutionized the manufacturing process. By enhancing precision, increasing production speed, reducing costs, and improving safety and sustainability, automation is shaping the future of the industry. As technology continues to evolve, it is likely that automation will become even more sophisticated, providing manufacturers with more opportunities to improve their operations and meet the growing demands of global markets.
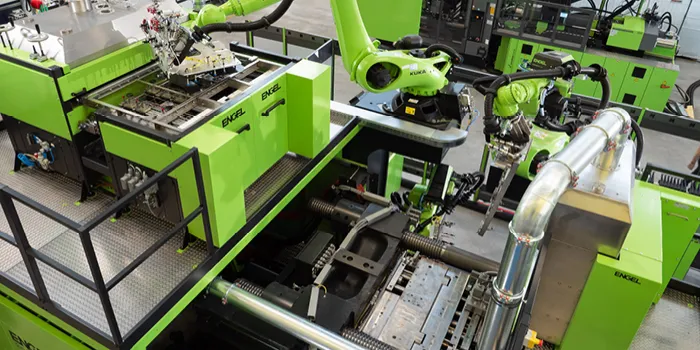