The automotive industry is under continuous pressure to improve fuel efficiency, reduce emissions, and enhance vehicle performance. One effective approach to achieving these goals is weight reduction. Thin-wall molding, a specialized injection molding process, plays a critical role in manufacturing lightweight plastic components without compromising strength or functionality.
What is Thin-Wall Molding?
Thin-wall molding refers to the process of injecting plastic into a mold with a wall thickness of less than 1 mm for small parts, or less than 2.5 mm for larger parts. This technique enables the production of lighter parts with shorter cycle times, thanks to faster cooling and material solidification.
Benefits in Automotive Applications
Weight Reduction
Lighter components contribute to improved fuel efficiency and lower CO₂ emissions. Thin-wall parts significantly reduce the overall weight of vehicles.Design Flexibility
Thin-wall molding allows intricate geometries and complex shapes, enabling integration of multiple functions into single components.Material Efficiency
Less material usage leads to cost savings and reduces environmental impact during manufacturing.Faster Production Cycles
Reduced cooling time means quicker cycle times and higher productivity, ideal for high-volume automotive manufacturing.Enhanced Aesthetics and Precision
Thin-wall parts typically have excellent surface finish and dimensional accuracy, meeting the visual and functional requirements of modern vehicle interiors and exteriors.
Common Automotive Components Made with Thin-Wall Molding
Dashboard and interior trims
Air vents and ducting systems
Battery casings for EVs
Headlamp housings
Under-hood components
Materials Used
Thin-wall molding requires materials with high flowability and good mechanical strength. Common materials include:
Polypropylene (PP)
Polyamide (PA)
Acrylonitrile Butadiene Styrene (ABS)
Polycarbonate (PC)
Thermoplastic composites for enhanced stiffness
Challenges and Solutions
Filling Thin Cavities: High injection speeds and pressures are needed; advanced simulation software helps optimize mold design.
Material Selection: Requires precise matching of material properties with design needs.
Mold Design Complexity: Sophisticated tooling and cooling strategies are essential for uniform thickness and dimensional stability.
Future Trends
Integration with Lightweight Composites: Combining thin-wall molding with fiber-reinforced materials to further reduce weight.
Electric Vehicle (EV) Innovation: Increased demand for thin-wall parts in battery enclosures and thermal management systems.
Sustainable Materials: Use of bio-based and recycled polymers for environmentally friendly automotive solutions.
Conclusion
Thin-wall molding is revolutionizing how lightweight, high-performance automotive parts are designed and produced. With continued material advancements and smarter mold technologies, it will remain a cornerstone in the quest for greener, more efficient vehicles.
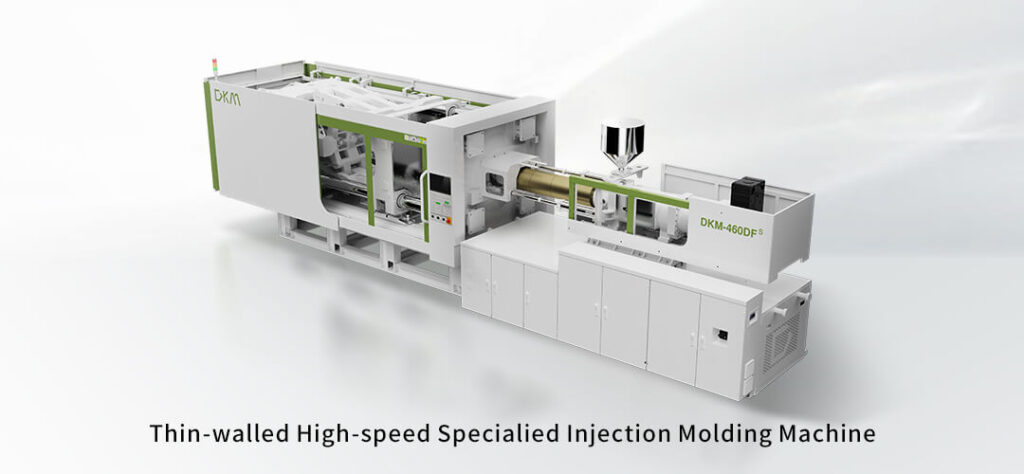