Two-shot molding, also known as dual-shot or multi-shot injection molding, is an advanced manufacturing process that allows for the production of complex plastic components with two distinct materials or colors in a single molding cycle. This technique is particularly advantageous in the automotive industry, where functionality, aesthetics, and cost-efficiency are critical.
What is Two-Shot Molding?
In two-shot molding, two different thermoplastics are injected into a mold in two separate stages but during one continuous cycle. The first material is injected into a mold to form the base component. Once it partially cools, the mold rotates or shifts, and a second material is injected either over or adjacent to the first material. This results in a single, integrated component with distinct areas of different materials or textures.
Benefits for Automotive Applications
Enhanced Aesthetics
Two-shot molding enables the seamless combination of glossy and matte finishes, or hard and soft surfaces, to create a visually appealing, tactile component such as interior trims, dashboard buttons, and control knobs.
Improved Functionality
The process allows engineers to integrate hard plastics with soft-touch materials like TPE (thermoplastic elastomers), improving grip, comfort, and noise reduction—key factors in ergonomic and user-friendly automotive interiors.
Durability and Reliability
Dual-material bonding achieved through two-shot molding is stronger and more consistent than traditional assembly methods using adhesives or mechanical fastening. This is especially beneficial in high-vibration automotive environments.
Cost Efficiency
Producing parts in a single molding process reduces the need for secondary operations like assembly, gluing, or painting. This results in faster production cycles and reduced labor and tooling costs.
Design Flexibility
Engineers can experiment with contrasting colors, textures, and materials to achieve both aesthetic appeal and high performance, such as in steering wheel controls, gear knobs, and HVAC vents.
Common Automotive Components Using Two-Shot Molding
Dashboard and center console components
Air vent louvers and trim bezels
Door handles and armrests
Climate control knobs
Steering wheel inserts
Sealing gaskets integrated with rigid housings
Materials Used
Common material pairings include:
PC/ABS + TPE: For high-impact strength with a soft-touch surface
Nylon + Rubber: For components requiring flexibility and chemical resistance
PP + TPE: For cost-effective, lightweight interior components
Conclusion
Two-shot molding is revolutionizing the way automotive manufacturers approach component design and production. By enabling the integration of dual textures and materials in a single, highly automated process, it enhances product quality, aesthetics, and production efficiency. As consumer expectations and regulatory standards continue to rise, this molding technique is becoming indispensable for delivering next-generation automotive interiors.
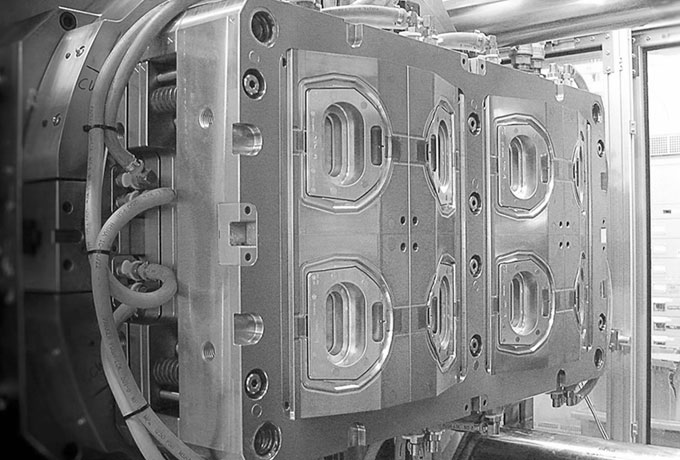