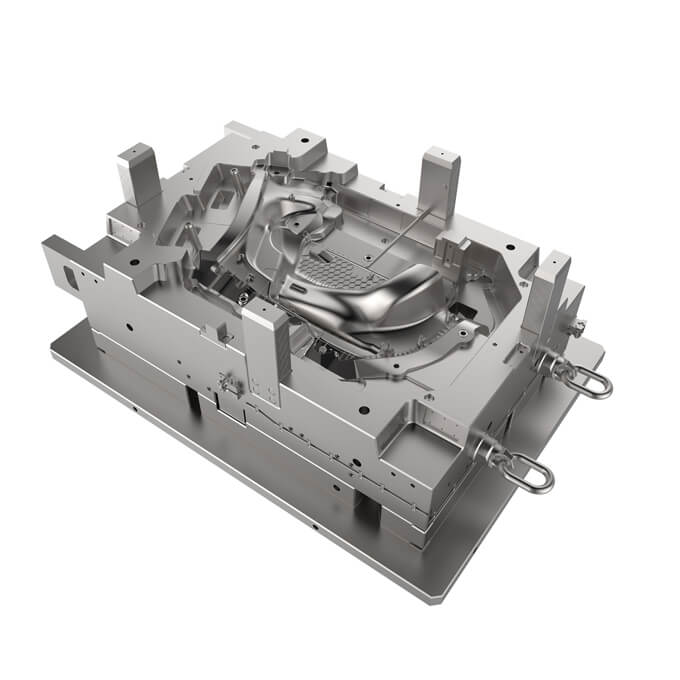
Injection Molds
Injection molds are the most commonly used in automotive production, particularly for plastic components such as dashboards, bumpers, and trim panels. These molds are designed to shape molten plastic by injecting it into a cavity under high pressure. They allow for high precision and repeatability, making them ideal for large-scale production. Multi-cavity injection molds can produce several identical parts simultaneously, increasing efficiency.
Compression Molds
Compression molds are used for shaping thermosetting plastics and composites, such as those found in structural components or under-the-hood parts. In this process, the material is placed into a heated mold cavity and compressed under high pressure to form the desired shape. Compression molds are suitable for parts requiring high strength and durability, such as brake components and engine covers.
Blow Molds
Blow molds are employed to create hollow automotive components like fuel tanks, air ducts, and fluid reservoirs. This process involves inflating heated plastic into a mold cavity to take its shape. Blow molding is particularly useful for producing lightweight and uniform hollow parts, contributing to improved fuel efficiency and overall vehicle performance.
Die Casting Molds
Die casting molds are used for shaping metal components such as engine blocks, transmission cases, and structural parts. This process involves injecting molten metal, typically aluminum or magnesium alloys, into a metal mold under high pressure. Die casting molds produce high-strength, detailed parts and are ideal for applications requiring precision and durability.
Rotational Molds (Rotomolds)
Rotational molds are used for creating large, hollow parts such as storage tanks and specialized containers. The process involves rotating a mold containing PVC or other thermoplastics to distribute the material evenly along the mold walls. Rotomolding is suitable for low-volume production and parts requiring seamless construction.
Extrusion Molds
Extrusion molds are utilized to produce continuous, linear automotive parts like weatherstrips, seals, and piping. In this process, the material is forced through a die to create a consistent cross-sectional shape, which is then cut to the desired length. Extrusion molds are ideal for high-volume production of uniform components.
Transfer Molds
Transfer molds are similar to compression molds but allow for better control over material flow. They are used to produce intricate parts such as electrical components, switches, and connectors. The process involves transferring the material into a heated mold cavity, ensuring accurate shaping and minimal waste.