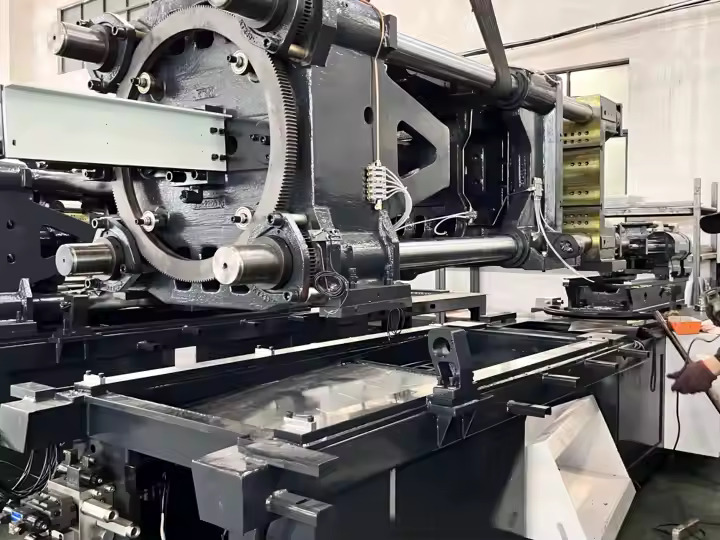
Injection Molding
Injection molding is one of the most common techniques for shaping PVC into complex and detailed parts. The process involves melting PVC resin and injecting it into a pre-designed mold cavity under high pressure. Once cooled, the molded part is ejected, ready for finishing. Injection molding is ideal for high-volume production of precision components such as automotive parts, medical devices, and household goods. It offers excellent consistency, tight tolerances, and rapid production cycles, making it a go-to method for manufacturers.
Extrusion Molding
Extrusion molding is used to create continuous lengths of PVC products with consistent cross-sections, such as pipes, tubing, and window frames. In this process, PVC material is heated and forced through a die to form a continuous shape, which is then cooled and cut to the desired length. Extrusion is highly efficient and cost-effective for producing large quantities of simple, linear products with uniform properties.
Blow Molding
Blow molding is employed to produce hollow PVC parts, such as bottles, containers, and tanks. In this technique, heated PVC is placed into a mold and inflated using air pressure to conform to the mold’s shape. Blow molding is particularly effective for creating lightweight, durable hollow structures with uniform wall thickness, making it ideal for applications in packaging, automotive fluid reservoirs, and more.
Compression Molding
Compression molding involves placing PVC material into a heated mold cavity, where it is compressed under high pressure to fill the mold and take its shape. This technique is suitable for manufacturing large, solid PVC parts or components with intricate details, such as electrical insulators and heavy-duty automotive parts. While slower than injection molding, compression molding is advantageous for low-volume production and certain specialized applications.
Rotational Molding (Rotomolding)
Rotational molding is used to produce hollow, seamless PVC products such as tanks, playground equipment, and large containers. In this process, PVC powder is placed inside a mold, which is heated and rotated on multiple axes. The heat melts the PVC, evenly coating the interior surfaces of the mold to create a uniform thickness. Rotomolding is ideal for producing large, durable parts with complex shapes and consistent wall thickness.