Injection molding is a popular manufacturing process used to produce a wide range of products, from small parts to large components, typically made of plastic. One of the most critical factors in injection molding is cycle time. It refers to the amount of time it takes to complete one full cycle of the injection molding process — from the moment the mold is closed until it is ejected. Understanding and optimizing cycle time is essential for improving productivity, reducing costs, and ensuring product quality. Here’s a breakdown of the different stages involved in the injection molding cycle and factors that affect cycle time.
1. The Stages of the Injection Molding Cycle
The injection molding cycle can be broken down into several stages:
a) Clamping
The mold halves are brought together with force, and the clamping mechanism is activated. The clamping force ensures the mold remains closed under the pressure of the injected material. The clamping stage typically takes just a few seconds but is critical for the overall cycle.
b) Injection
In this stage, plastic (or another material) is melted in a barrel and then injected into the mold cavity under high pressure. The injection stage can take anywhere from a few seconds to a minute, depending on the complexity and size of the part being produced. The injection time directly impacts the cycle time and is influenced by factors like material flow, part geometry, and the required mold temperature.
c) Cooling
Once the mold cavity is filled with the molten material, the part begins to cool and solidify. Cooling is typically the longest part of the cycle because the part needs to be cool enough to hold its shape when ejected from the mold. The cooling time is highly dependent on the material, part thickness, mold design, and cooling system efficiency. Faster cooling can reduce cycle time but might lead to issues like warping or poor surface finish.
d) Mold Opening and Ejection
After the part has cooled sufficiently, the mold opens, and the molded part is ejected from the cavity. The opening of the mold is typically a fast action, but the ejection time can vary depending on the part’s geometry and any secondary processes that may be required (e.g., trimming or removing inserts).
e) Mold Closing
Once the part is ejected, the mold closes again, and the cycle begins anew. This final stage includes any additional checks or operations that need to take place before the process can restart.
2. Factors Affecting Injection Molding Cycle Time
Several factors can impact the overall cycle time in injection molding:
a) Material Type
Different materials have different melting temperatures and cooling rates, which affect how long it takes for them to fill the mold and solidify. For example, thermoplastics generally cool faster than thermosets, affecting the time spent in the cooling stage.
b) Part Geometry
Complex part shapes with thin walls or intricate details may take longer to cool and require more precise injection to ensure complete filling. Parts with simple geometries tend to have shorter cycle times.
c) Mold Design
The design of the mold, including its cooling channels, gate size, and runner system, significantly affects the cycle time. Efficient mold designs ensure faster injection, better cooling, and overall reduced cycle times.
d) Machine Speed and Parameters
The performance of the injection molding machine also plays a key role in determining cycle time. Machines with higher injection speeds, faster mold clamping times, and advanced cooling systems can help shorten the overall cycle time. Machine parameters such as injection pressure, temperature settings, and speed of movement (e.g., for clamping and ejection) all influence the cycle duration.
e) Cooling System Efficiency
Effective cooling is crucial for minimizing cycle time. The use of advanced cooling systems (such as conformal cooling channels) and optimizing the mold temperature can significantly reduce the cooling time, which is often the longest phase of the injection molding process.
f) Ejection Force and Timing
The time it takes to eject the part and the force needed can also affect the cycle. If a part requires additional actions like trimming, inserting, or secondary operations, it can increase the overall cycle time.
g) Temperature Control
Both mold temperature and material temperature play a role in determining cycle time. Higher mold temperatures can reduce the viscosity of the molten plastic, leading to faster filling times, but may increase cooling times. Balancing these temperatures is key to reducing cycle time while maintaining product quality.
3. Optimizing Injection Molding Cycle Time
Reducing cycle time without sacrificing quality or product integrity is crucial for manufacturers to stay competitive. Here are some strategies for optimizing cycle time:
a) Optimize Mold Design
Improving mold cooling efficiency by designing better cooling channels or using advanced cooling technologies can drastically reduce cooling time, which is often the longest phase of the cycle. Proper venting is also important to avoid trapped air and reduce defects.
b) Improve Material Flow
Selecting the appropriate materials with better flow characteristics for a given part design can reduce the time it takes to fill the mold cavity. Moreover, optimizing injection speed and pressure helps ensure quick and efficient filling of the mold.
c) Machine Tuning
Adjusting the injection molding machine parameters, such as injection speed, pressure, and temperature, helps improve efficiency. Proper calibration of the machine ensures each stage of the process operates optimally, leading to shorter cycle times.
d) Use of Additives
Incorporating additives like nucleating agents can enhance the crystallization speed of materials, reducing cooling time. Some additives can also improve the flow properties of the material during injection, helping to achieve faster filling times.
e) Part Design Modifications
Simplifying the design of the part (e.g., reducing wall thickness and avoiding complex geometries) can lead to reduced cycle times. However, these changes need to be balanced with the functional requirements of the part.
f) Use of Multi-Cavity Molds
Using multi-cavity molds can increase the production rate per cycle by allowing multiple parts to be produced simultaneously, thus improving overall cycle time per part.
4. Impact of Cycle Time on Cost and Production Efficiency
Cycle time directly impacts both the cost and efficiency of injection molding. Shorter cycle times result in higher production rates, which can lower the per-unit cost of each part. However, focusing solely on minimizing cycle time without considering quality or the complexity of the part can lead to defects, rework, and reduced overall profitability.
By carefully balancing all factors — material, machine, mold design, and part complexity — manufacturers can achieve an optimized cycle time that ensures both quality and cost-efficiency.
5. Conclusion
Understanding injection molding cycle time is essential for manufacturers looking to improve their production processes. By understanding the factors that influence cycle time and employing strategies to optimize them, manufacturers can improve their overall efficiency, reduce production costs, and deliver high-quality products to the market in a timely manner. Continuous monitoring, optimization, and innovative techniques will further enhance cycle time and ensure the long-term success of the injection molding process.
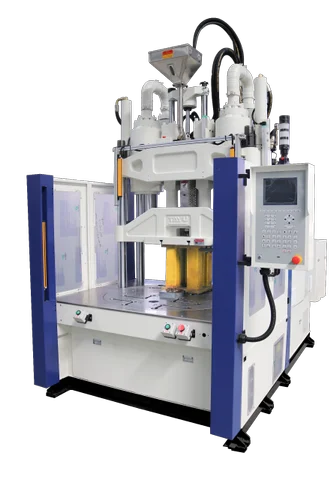