Injection molding is a widely used manufacturing process for producing plastic parts with high precision and efficiency. However, the base polymer alone may not always meet the specific mechanical, thermal, or aesthetic requirements of an application. To tailor material properties to meet diverse performance criteria, additives are commonly incorporated into the polymer resin prior to or during the injection molding process.
- Purpose of Additives in Injection Molding
Additives serve to:
- Improve mechanical strength, durability, or flexibility.
- Enhance thermal stability or resistance to UV radiation.
- Alter surface appearance or color.
- Provide flame retardancy, antimicrobial properties, or antistatic behavior.
- Aid in processing by improving flow or reducing cycle times.
- Common Types of Additives and Their Functions
Additive Type | Function |
Plasticizers | Increase flexibility and reduce brittleness. |
Reinforcing Fillers | Improve strength, stiffness, and dimensional stability (e.g., glass fibers). |
UV Stabilizers | Prevent degradation from UV light exposure. |
Flame Retardants | Reduce flammability and improve fire resistance. |
Colorants/Pigments | Provide specific colors or aesthetic effects. |
Antioxidants | Prevent thermal oxidation during processing or service life. |
Antimicrobials | Inhibit microbial growth on the molded part. |
Lubricants | Improve mold release and flow during processing. |
Antistatic Agents | Minimize static electricity build-up. |
- Incorporation Methods
Additives are typically incorporated into the polymer using:
- Masterbatches: Concentrated mixtures of additives in a carrier resin.
- Direct blending: Physical mixing of additives with the polymer pellets.
- Compounding: Melt-mixing polymers and additives before pelletizing for molding.
- Considerations for Additive Selection
When choosing additives, manufacturers must consider:
- Compatibility with the base resin.
- End-use environment (e.g., exposure to heat, light, chemicals).
- Regulatory compliance, especially for medical or food-contact applications.
- Cost-effectiveness and impact on cycle times and mold wear.
- Examples of Enhanced Applications
- Automotive components: Use of glass fiber reinforcement for structural integrity.
- Outdoor furniture: UV stabilizers for long-term weather resistance.
- Consumer electronics: Flame retardants for safety compliance.
- Medical devices: Antimicrobial additives for hygiene.
- Emerging Trends
- Sustainable additives: Derived from bio-based or recycled sources.
- Smart additives: That provide self-healing, color-changing, or conductive properties.
- Nanocomposites: Use of nano-additives to significantly enhance properties without high filler loading.
Conclusion
The use of additives in injection molding enables manufacturers to go beyond the inherent limitations of base polymers, allowing for customization of product performance, durability, and appearance. With advancements in material science, the strategic use of additives continues to open new possibilities in plastic part design and functionality.
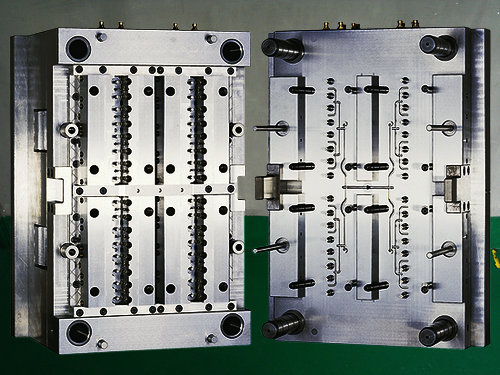