Injection molds are critical components in the plastic manufacturing industry, often representing significant investments in time and cost. Over time, however, molds are subjected to wear and tear that can degrade their performance, affect part quality, and shorten their lifespan. Understanding the causes of wear and implementing strategies for prevention are essential for maintaining production efficiency and reducing operational costs.
Causes of Wear and Tear in Injection Molds
Abrasive Wear
Occurs when hard particles in the plastic resin (like glass fibers or mineral fillers) scratch or grind the mold surface.
Common in the molding of filled or reinforced plastics.
Adhesive Wear (Gallings)
Results from material transfer between the mold surface and the plastic due to sticking and sliding action.
Often found in high-pressure or poorly lubricated areas.
Corrosive Wear
Caused by chemical reactions between the mold material and aggressive chemicals in certain resins (e.g., PVC, flame retardants).
Can lead to pitting and surface degradation.
Thermal Fatigue
Repeated heating and cooling cycles induce thermal stress, leading to micro-cracks and surface spalling.
Accelerated in molds with poor temperature control or uneven cooling.
Mechanical Fatigue
Continuous opening and closing of molds, as well as ejector system actions, can lead to fatigue failures.
Common in high-volume production environments.
Poor Mold Maintenance
Lack of regular cleaning, lubrication, and inspection accelerates degradation.
Residue build-up can also affect part quality and cause mechanical issues.
Prevention Strategies
Material Selection
Use high-quality mold steels with appropriate hardness and corrosion resistance (e.g., H13, P20, stainless tool steels).
Apply surface treatments like nitriding, chrome plating, or PVD coatings to enhance durability.
Optimized Mold Design
Ensure smooth flow paths to minimize turbulence and shear.
Incorporate wear-resistant inserts in high-stress areas.
Design for uniform cooling to reduce thermal fatigue.
Controlled Processing Conditions
Maintain optimal temperature and pressure to reduce stress on the mold.
Use appropriate injection speed and clamping force settings.
Material Handling and Preparation
Properly dry and filter resin to remove contaminants and moisture.
Avoid using overly abrasive or corrosive fillers when not necessary.
Regular Maintenance and Monitoring
Establish a preventive maintenance schedule that includes cleaning, inspection, lubrication, and part replacement.
Use sensors and monitoring tools to track wear patterns and mold conditions.
Training and Best Practices
Educate operators and technicians on mold care and correct handling procedures.
Encourage immediate reporting of issues to prevent further damage.
Conclusion
Wear and tear in injection molds is inevitable, but its impact can be significantly reduced through smart design, material choice, process optimization, and consistent maintenance. By proactively addressing these challenges, manufacturers can extend mold life, ensure product quality, and maintain cost-effective operations.
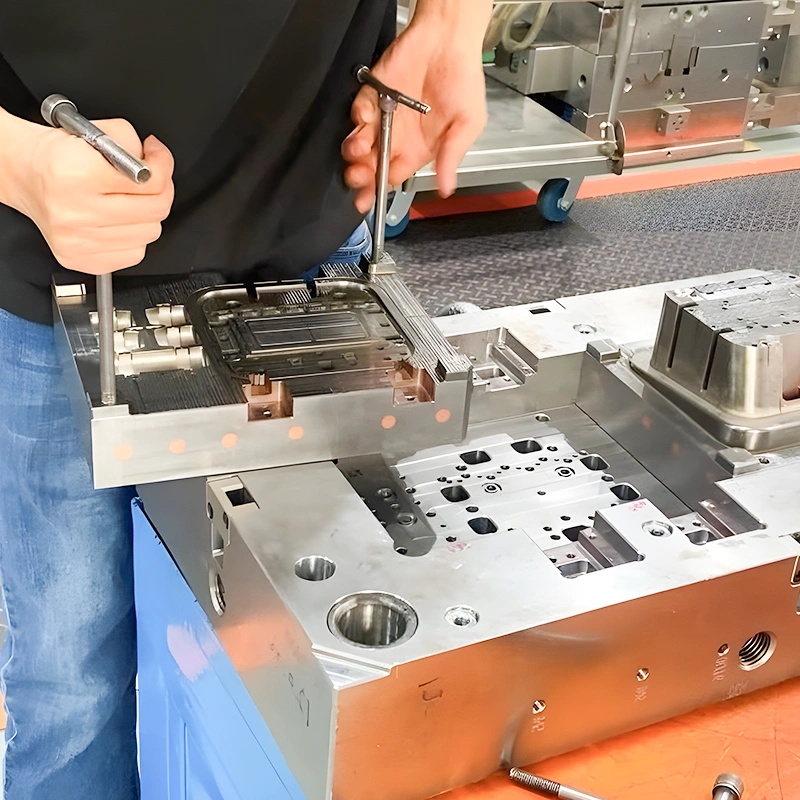